Warehousing decisions directly shape how smoothly your Shopify store fulfills orders, manages stock, and handles customer expectations. Operations stall, especially during growth phases, without a system built for accuracy and speed.
A Statista report suggests that nearly 50% of U.S. online shoppers have abandoned a purchase due to slow delivery timelines.
With the right warehouse management system (WMS), you’re not just getting more software. It’s about solving the core fulfillment challenges before they impact your revenue and customer loyalty.
But, before investing, you need to assess if a WMS fits your current operations or if it’s something you’re planning ahead for.
- What Is a WMS (Warehouse Management System) for Shopify?
- Top Signs You’ve Outgrown Manual Warehouse Processes
- Must-Have WMS Features for Shopify Merchants
- WMS Needs by Business Size
- Common Mistakes When Choosing a Shopify WMS
- Where Kladana Fits in the Shopify Fulfillment Workflow
- Final Thoughts: Choose a WMS That Fits Your Growth
- FAQs
- List of Resources
What Is a WMS (Warehouse Management System) for Shopify?
A warehouse management system (WMS) helps businesses control and optimize daily operations. For Shopify merchants, this means having a system that tracks how inventory moves through storage locations, manages picking and packing workflows, and provides real-time stock visibility to keep Shopify inventory accurate.
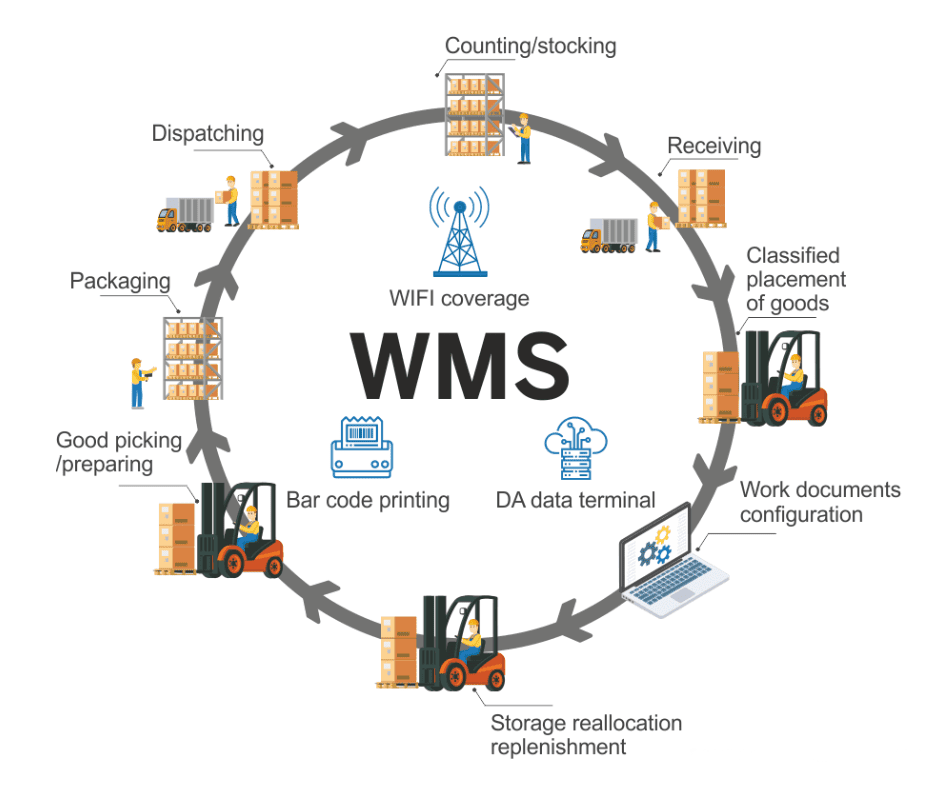
Unlike general inventory systems, a WMS focuses directly on warehouse processes. It’s the link between your digital storefront and the physical movements of products which involves receiving goods and making outbound fulfillment.
The Shopify WMS integration lets store owners and warehouse managers reduce picking errors, improve stock accuracy, and speed up the entire fulfillment cycle.
But choosing a WMS depends on how complex your warehouse needs actually are and it should not be confused with an Order Management System (OMS).
Feature Area | Inventory System | Order Management System (OMS) | Warehouse Management System (WMS) |
Primary Function |
Track stock levels and product availability |
Manage order routing, fulfillment, and returns |
Manage warehouse operations and stock movement within storage zones |
Focus |
What’s in stock? |
What’s ordered and where should it go? |
Where is stock stored and how is it handled? |
Key Workflows |
Stock counts, reorder alerts |
Order processing, shipping labels, returns |
Receiving, put-away, picking, packing, and bin tracking |
Who Uses It |
Procurement, sales |
Sales, customer support, and fulfillment teams |
Warehouse staff, logistics managers |
Shopify Sync |
Update stock availability |
Syncs orders and fulfillment status |
Tracks warehouse stock and syncs movements to Shopify |
For Shopify merchants seeking a solution that bridges the gap between inventory management and full-fledged warehouse operations, Kladana offers a comprehensive platform. You get a blend of inventory tracking, order processing, and essential warehouse functionalities like bin storage and barcode scanning.
When a Shopify Store Might Need a WMS
Implementing a WMS becomes crucial when:
- Order volume increases and manually maintaining daily stock in Excel becomes unsustainable.
- There are multiple storage locations, and tracking inventory across various warehouses or storage areas requires centralized control.
- You have a complex picking and packing process where handling diverse product ranges necessitates organized picking and packing processes.
- Real-time inventory visibility is needed, and accurate, up-to-the-minute stock information is essential to prevent overselling.
- You experience a need for operational efficiency by automating routine warehouse tasks to reduce errors and labor costs.
Artisanté streamlined their manufacturing management in half a year using Kladana. The transition allowed them to handle multiple warehouse zones and drive team efficiency with a scalable WMS solution.
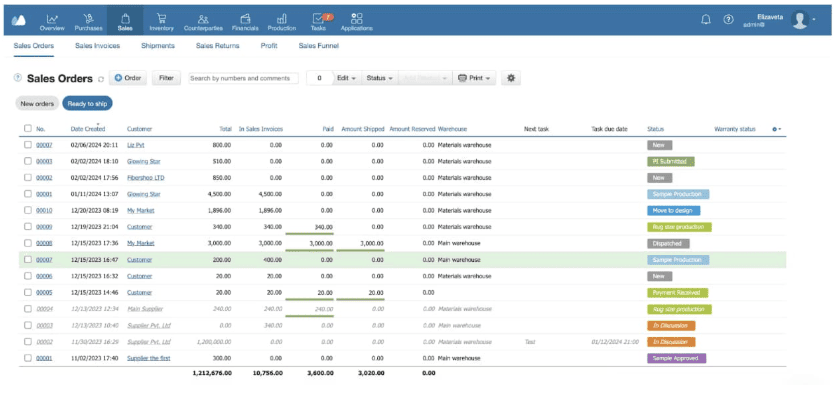
They have unified warehousing, barcoding, sales, and financial insights within a single platform for better operational efficiency.
Top Signs You’ve Outgrown Manual Warehouse Processes
You can manage inventory manually for a while, but rising order volumes, increased returns, and warehouse confusion start costing real money. If these issues are becoming familiar, it’s time to reconsider your warehouse setup.
1. Slow fulfillment and growing returns
Any delay in order fulfillment can make customers unhappy, and you may experience higher return rates. And these mistakes multiply when warehouse teams rely on printed pick lists or manual stock checks.
So, when products ship late, wrong items reach customers, and reverse logistics start eating into margins. A WMS for Shopify helps automate picking routes, reduce handling time, and minimize incorrect shipments.
2. Inventory mismatches
You may see inventory appear “in stock” online, but unavailable on warehouse shelves, which can lead to overselling and order cancellations. Without real-time stock movement tracking, manual updates quickly fall out of sync.
A Shopify warehouse management system ensures that stock levels remain accurate across storage zones, preventing lost sales and frustrated customers.
3. Wasted warehouse space
Products often become scattered or stored inefficiently without proper bin storage and tracking. Teams spend extra time locating items, and valuable space goes unused.
A WMS introduces bin-level tracking and optimized put-away strategies, helping businesses use their storage capacity more effectively.
4. Lack of task tracking or barcode scanning
Manual picking lists and verbal task assignments create confusion on the warehouse floor. Without barcode scanning or digital task management, it is impossible to monitor who picked which order, where errors occurred, or how fast tasks are completed.
5. No visibility on worker productivity
Understanding workforce productivity becomes a guessing game without clear task assignments and performance metrics.
Cura Pharmaceuticals faced challenges with data accuracy and business workflows. By adopting Kladana, they increased data accuracy and streamlined their business processes within six months, demonstrating the impact of moving beyond manual systems.
Must-Have WMS Features for Shopify Merchants
Features aren’t just technical checkboxes; they shape how quickly orders move through your warehouse and how accurately inventory syncs with Shopify.
Feature | How It Helps |
Bin-level tracking |
Assigning products to specific bins or shelves reduces search time and improves space utilization. |
Barcode scanning |
Accelerating receiving, picking, and packing while minimizing manual errors. |
Multi-location inventory |
Consolidating stock visibility across multiple warehouses or zones, keeping Shopify inventory accurate. |
Real-time stock movement |
Updates inbound and outbound stock instantly to avoid overselling and ensure order accuracy. |
Picking and packing workflows |
Guides warehouse staff through efficient picking routes and organized packing to speed up fulfillment. |
Inventory receipts and transfers |
It helps simplify the recording of new stock arrivals and internal stock transfers between warehouse zones. |
Warehouse task automation |
Assigns and tracks picking, packing, and inventory checks, improving task accountability. |
Warehouse zones & tasks |
Enables clear assignment of picking, receiving, and auditing activities by warehouse area, improving workflow management. |
Shopify order sync |
Keeps stock levels aligned in real time between the warehouse and Shopify storefront to prevent overselling. |
Stock transfers |
Manages inventory movement between locations or zones without manual spreadsheets, crucial for multi-location setups. |
Shopify WMS integration |
Connects warehouse data directly with Shopify to sync stock, order status, and fulfillment updates. |
Solutions like Kladana combine essential warehouse features with inventory and order management. It helps Shopify merchants streamline back-end operations without the cost of complex enterprise systems.
WMS Needs by Business Size
As your business moves from early growth to high-volume operations, warehouse management must change. What starts with a simple inventory control system soon requires barcode scanning, stock transfers, and zone management to maintain efficiency.
Choosing the right WMS depends on how complex your fulfillment processes are and how fast you plan to scale.
Starter Store
Most operations at this stage happen from a single location, often using manual methods.
- Simple stock control with basic tracking of product quantities.
- Manual bins or shelves without location mapping.
- May not need a dedicated WMS yet. Spreadsheets or basic inventory tools are often sufficient.
WMS Role: Often not required at this stage. A basic inventory system is usually enough if order volumes are low and space is limited.
Growing Brand
With a dedicated warehouse space and rising order volumes, warehouse processes need better control.
- Small warehouses require organized storage to avoid stockouts.
- Barcode scanning to minimize picking and packing errors.
- Stock transfers between storage zones or shelves to optimize space usage.
WMS Role: Barcode scanning becomes essential to reduce picking errors. Stock transfers between areas or shelves help optimize limited space.
Scaling Business
High order volumes and multiple storage locations require advanced warehouse oversight.
- Multiple warehouse zones or teams handling different fulfillment stages.
- Real-time dashboards to track stock movements and operational performance.
- Detailed warehouse metrics to monitor worker productivity and optimize picking and packing workflows.
WMS Role: Real-time dashboards help manage inventory across zones. Managers require access to detailed warehouse metrics, stock movements, and worker productivity tracking.
Common Mistakes When Choosing a Shopify WMS
Choosing a warehouse management system without a clear understanding of your operational needs often leads to wasted time, poor system adoption, and unnecessary expenses.
Mistakes made at this stage affect budgets, disrupt fulfillment workflows, and create bigger problems later.
Avoid these common pitfalls:
1. Confusing WMS with Inventory Software
A WMS handles warehouse workflows like picking, packing, and task assignments. Inventory software primarily tracks stock availability and reorder levels.
Many Shopify merchants invest in inventory tools expecting warehouse control features, only to realize later that critical functions like bin tracking or barcode scanning are missing.
2. Choosing Tools Without Shopify-Specific Integration
Not all WMS platforms connect smoothly with Shopify. Some require complex custom integrations, which delay deployment and increase costs. Always check for direct Shopify WMS integration that supports real-time stock updates and order syncing without manual intervention.
3. Overinvesting Too Early
Buying a feature-heavy WMS before your business truly needs it leads to underutilized tools and higher monthly costs. Smaller teams don’t benefit from the Shopify ERP system if the basics of stock control aren’t yet in place.
4. Not Planning for Returns or 3PL Handoffs
When selecting a WMS, returns management and handling third-party logistics partners are often overlooked. Without proper return workflows and 3PL coordination, stock discrepancies and fulfillment delays become harder to avoid.
Ensure the system supports smooth inventory receipts for returned products and can integrate or share data easily with 3PL providers when needed.
Where Kladana Fits in the Shopify Fulfillment Workflow
Kladana offers a combined solution for inventory management, order processing, and essential warehouse controls. Sure, you don’t get full WMS capabilities like multi-warehouse bin-level sync with Shopify.
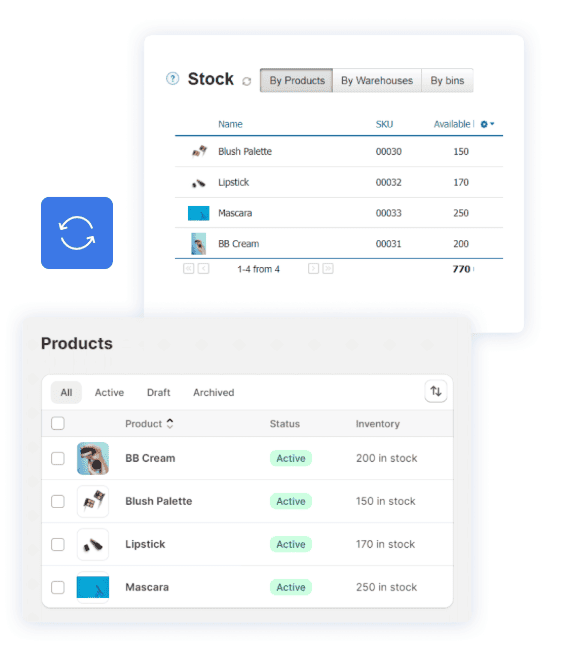
However, it does cover the core needs of growing Shopify businesses that want better stock accuracy without the complexity of an enterprise system.
Why Shopify Merchants Choose Kladana Over Complex WMS Tools:
✅ Real-Time Stock Tracking — Monitor inventory across your primary warehouse to maintain accurate stock levels at all times.
✅ Automated Order Processing — Eliminate repetitive tasks and speed up fulfillment with smart order workflows.
✅ Direct Shopify Sync — Keep your store’s product availability and stock status updated without manual edits.
✅ Zone-Based Warehouse Controls — Organize your warehouse into simple zones and track stock movements with ease.
✅ Barcode-Powered Accuracy — Use barcode scanning tools to boost picking precision and reduce order errors.
✅ Built for Growing Teams — Skip the complexity of enterprise WMS systems with a solution that’s easy to adopt and scale.
For businesses that have outgrown spreadsheets but aren’t ready for a complex WMS, Kladana provides the right balance of control and simplicity.
Final Thoughts: Choose a WMS That Fits Your Growth
A full warehouse management system isn’t always the first move a Shopify business needs to make.
Start by asking what’s holding back your current fulfillment process — is it speed, stock accuracy, or lack of visibility?
Invest in tools that solve those immediate challenges without overcomplicating operations. As your order volumes grow and warehouse complexity increases, a WMS will naturally become part of that progression.
Use this guide to assess where you stand today, what features actually matter, and how to avoid common missteps before committing to a system.
Discover how to streamline warehouse tasks and improve fulfillment accuracy. Ready to simplify operations? Book a Kladana demo today.
FAQs
Still figuring out if a WMS makes sense for your Shopify store? These answers might help.
Do Shopify stores really need a WMS?
If you’re managing a dedicated warehouse or struggling with stock accuracy, a WMS can improve operations.
Can I use inventory software instead of a WMS?
Inventory software tracks stock levels but doesn’t manage warehouse workflows like picking and packing.
When is it too early to invest in a WMS?
If you’re fulfilling orders from a small space and handling low daily volumes, it’s likely too soon.
Does Kladana offer a full WMS for Shopify?
Kladana provides core warehouse features but doesn’t offer full WMS functionality like advanced multi-warehouse sync yet.
What features should I prioritize in a Shopify Warehousing?
Focus on real-time stock updates, barcode scanning, warehouse task management, and Shopify integration.
How does a WMS Shopify improve order accuracy?
By guiding warehouse staff through structured picking and packing workflows, reducing errors.
Can a WMS handle returns and 3PL coordination?
Some WMS platforms support returns and integrate with 3PL systems; check for these before choosing.
Is Shopify’s native inventory management enough?
For basic operations, yes. But growing businesses often need more detailed warehouse and stock controls.
List of Resources
Statista — Leading reasons for abandonment during checkout in the U.S. 2024