Selecting the right costing approach isn’t just about tracking expenses — it’s a strategic lever that can boost profitability and streamline operations for manufacturing and inventory-driven businesses.
This article highlights essential cost estimation techniques and product costing systems, empowering you to better control expenses and maximize your financial outcomes. Explore practical guidance and insights into effective costing approaches to enhance your manufacturing and inventory management strategies.
- Understanding Costing Methods and Approaches
- Types of Costing Methods in Manufacturing
- Inventory Costing Methods
- Product Costing Systems and Techniques
- Cost Estimation Techniques
- Choosing the Right Costing Method for Your Business
- Common Mistakes in Product Costing and How to Avoid Them
- Frequently Asked Questions on Costing Methods and Approaches
Understanding Costing Methods and Approaches
A clear grasp of various costing methods helps businesses control their expenses and make effective decisions.
What is Costing?
Costing is figuring out how much it costs to produce goods or provide services. This includes all the expenses like raw materials, labor, utilities, and overhead costs. Accurate manufacturing cost calculation shows the true cost per unit of each product made. Using a suitable product costing process, businesses keep their finances clear and easy to manage. Good costing practices ensure a fair profit margin and accurate pricing.
Why Accurate Costing is Essential
Accurate costing directly affects how much money a business makes. Precise cost estimation techniques help set correct product prices that cover costs and provide profit. Poor costing can lead to underpricing or overpricing products, causing either lost revenue or lost customers. Correct costing also supports better decisions in purchasing, inventory management, and production planning. A strong cost estimation system helps businesses understand where they spend money and where they can save. This leads to improved operations and increased competitiveness in the market.
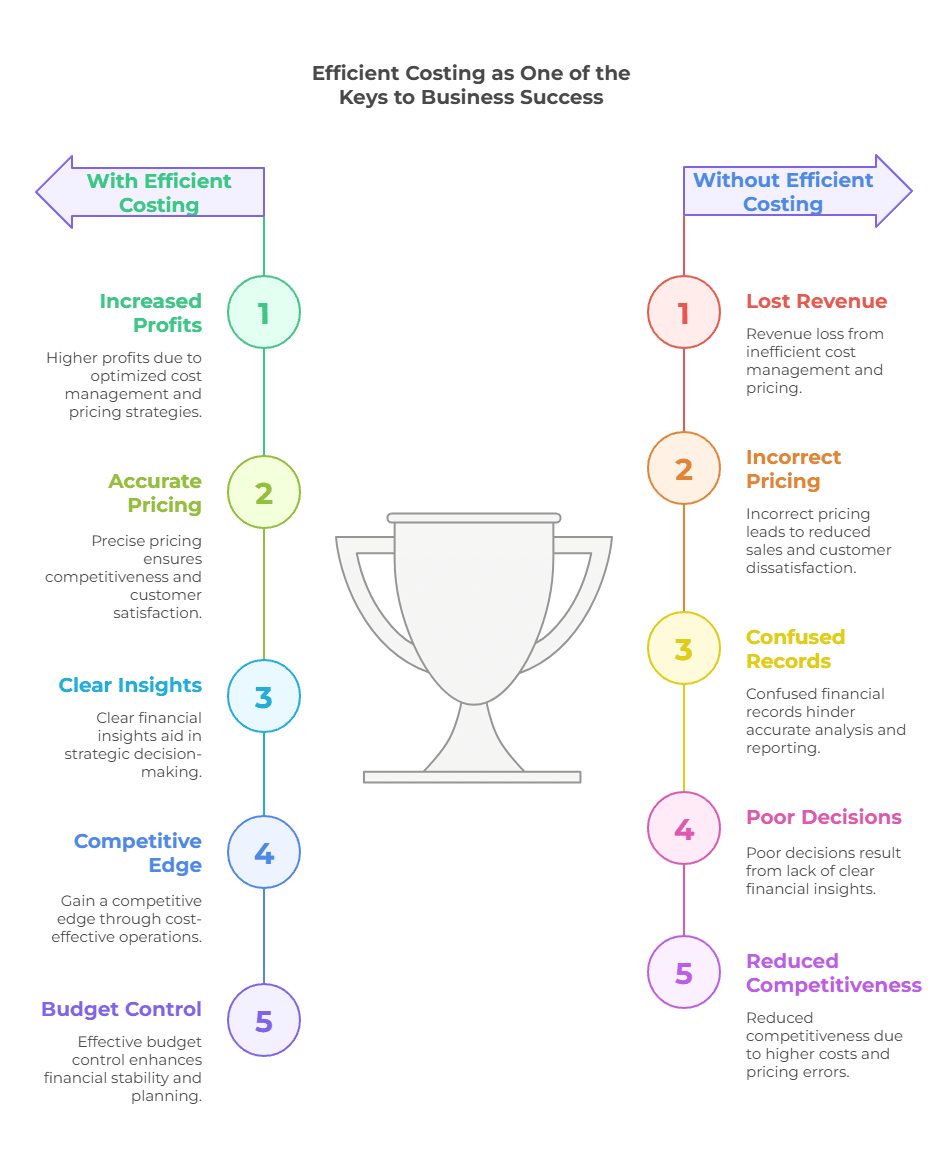
Types of Costing Methods in Manufacturing
Manufacturing businesses use several costing methods to track and control their production expenses effectively.
Job Costing
Job costing tracks expenses by individual job or project. Businesses using this method record costs separately for each custom order or unique project. Costs include labor, materials, and any special tools needed for the job.
This method suits companies producing custom goods, like tailored furniture or special equipment. Job costing gives clear insights into profitability per project, helping businesses manage budgets and improve pricing strategies.
Process Costing
Process costing evenly distributes costs across all units produced during a certain period. This approach works best for mass-produced products, like food items or beverages, where each unit is similar. It calculates the average cost per unit, and helps businesses manage pricing and production efficiently.
Companies using this product costing system gain consistent control over their manufacturing expenses.
Activity-Based Costing (ABC)
Activity-Based Costing (ABC) assigns expenses based on specific business activities. This method looks closely at each production step and overhead costs, such as machinery maintenance and administration. ABC is detailed and provides precise cost information. It is helpful for businesses aiming to reduce unnecessary spending and improve operational efficiency.
Companies using ABC understand exactly where their resources go, allowing better budget control and decision-making.
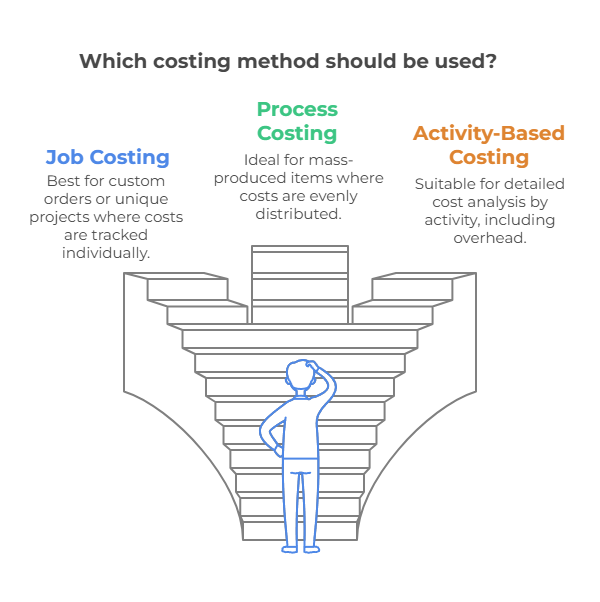
Inventory Costing Methods
Inventory costing helps businesses value their stock accurately, which affects financial statements and profitability.
First-In, First-Out (FIFO)
FIFO means that the oldest stock items are sold first. This approach aligns inventory costs with the actual order of product purchases. Businesses using FIFO reflect current market prices in their remaining inventory, which helps manage inventory values clearly and consistently. FIFO is popular due to its simplicity and transparency in tracking inventory costs.
Last-In, First-Out (LIFO)
LIFO method sells the newest inventory items first. Under this method, businesses match recent inventory costs to current sales. LIFO can lower taxable profits during inflation by increasing the cost of goods sold. Businesses should understand tax rules clearly before using LIFO, as it may not be accepted everywhere.
Weighted Average Cost (WAC)
Weighted Average Cost calculates inventory value using an average cost of all units available for sale. This method blends all costs together evenly, providing a balanced approach to valuing inventory. WAC is straightforward and useful for businesses with many similar inventory items. It simplifies inventory management and provides clear financial information.
📊 Automate Cost Calculation with Kladana ERP
Manual costing can be time-consuming and often inaccurate. Kladana helps you avoid this by automatically calculating your production costs — both before and after manufacturing.
💸 Planned Cost Report
Plan your production budget with confidence. Kladana creates a planned cost report using the details from your production order — like the list of materials (BOM) and operation rates. This report shows how much it should cost to make a product.
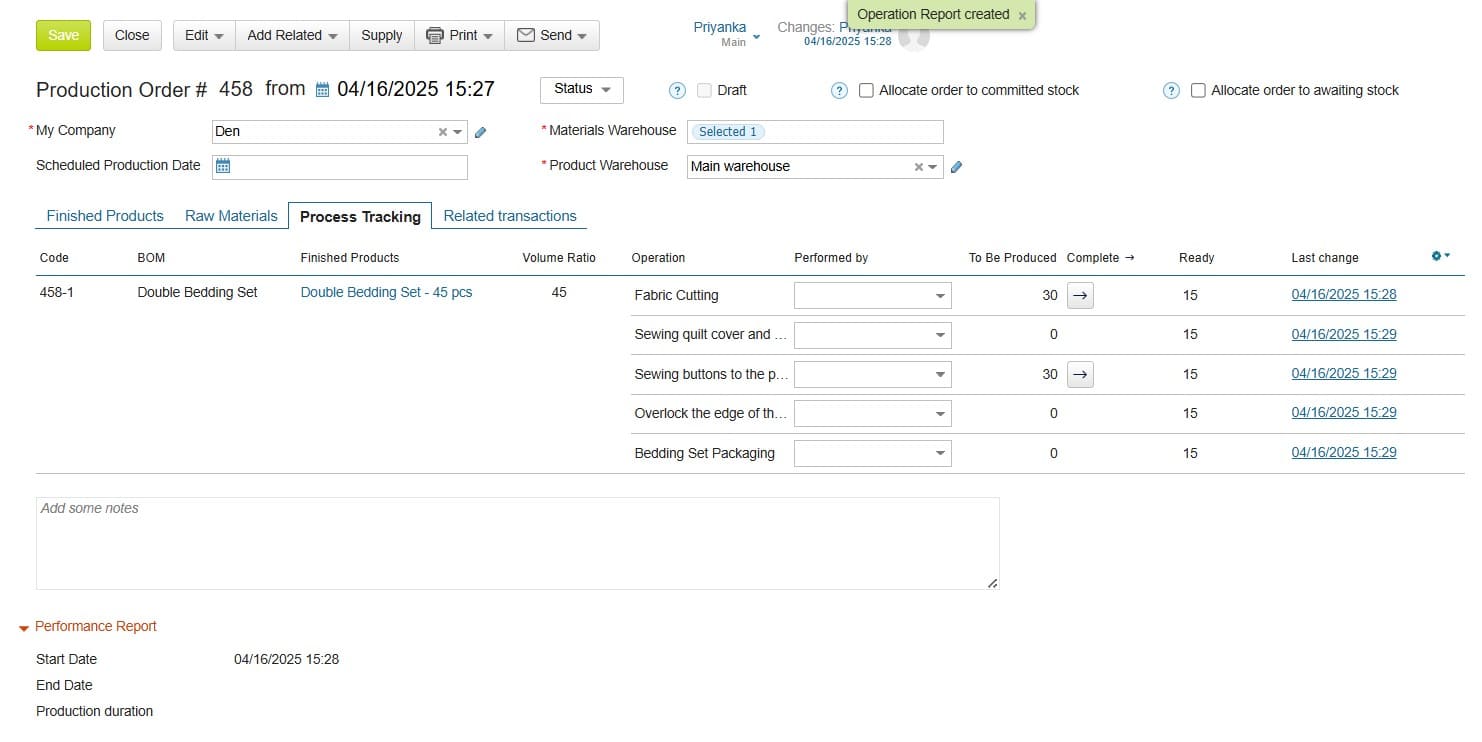
With the planned cost report, you can:
- See expected expenses before production starts
- Set realistic budgets and profit targets
- Prepare purchase plans for raw materials
- Compare planned vs. actual costs later
This helps you avoid surprises and manage your production more efficiently.
💸 Actual Cost of Goods
Track what your product really costs after production.
Kladana calculates the actual cost automatically by collecting data from all related transactions:
- Shipments
- Receivings
- Transfers
- Sales Returns
- Stock & Profit Reports
This helps you analyze profit margins, fine-tune pricing, and better control inventory value.
Product Costing Systems and Techniques
Businesses use different product costing systems and cost estimation techniques to manage expenses and boost efficiency.
Standard Costing
Standard costing uses predetermined costs for materials, labor, and overhead. Businesses set these costs in advance based on expected prices and efficiencies. By comparing actual costs to these standards, companies quickly spot variances.
This method helps identify areas needing improvement, control costs effectively, and enhance profitability.
Marginal Costing
Marginal costing focuses on variable costs directly tied to production. Fixed costs, like rent or salaries, are treated separately. This method helps businesses decide pricing and production volumes clearly.
Marginal costing is useful for evaluating how changes in sales affect overall profits, assisting managers in quick and informed decision-making.
Direct Costing
Direct costing involves assigning only costs that directly relate to product manufacturing. This includes expenses such as raw materials and direct labor. Overhead costs remain separate. Direct costing clearly identifies the exact production costs, aiding in precise pricing and cost control.
This method provides transparent insights into profitability for each product, improving strategic decisions.
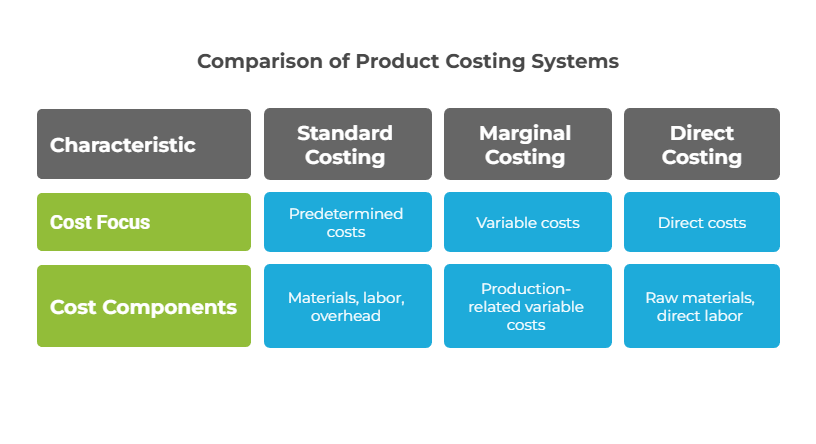
Cost Estimation Techniques
Accurate cost estimates help businesses manage budgets and avoid overspending in manufacturing and production.
Analogous Estimation
Analogous estimation uses historical data from similar past projects. Businesses compare previous project expenses with current needs. This method is quick and simple, suitable for early project planning when detailed data is limited.
Parametric Estimation
Parametric estimation uses statistical methods to calculate costs. Businesses use mathematical formulas based on known costs from previous projects. By adjusting for current project specifics, this method provides reliable cost estimates. It suits projects with predictable and repetitive tasks.
Bottom-Up Estimation
Bottom-up estimation calculates total costs by adding detailed individual costs from each task or component. Businesses estimate costs for each element separately, then sum these values to get the full project cost. This method is highly accurate and ideal for complex projects with clearly defined tasks.
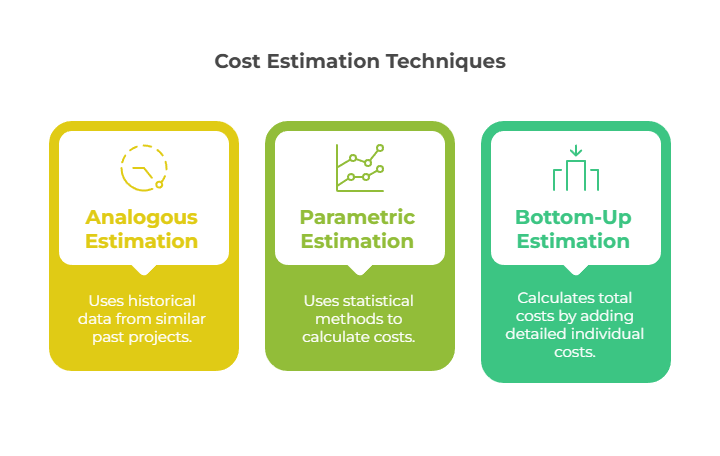
Choosing the Right Costing Method for Your Business
Picking the correct costing methods depends on your specific business situation and goals.
Assessing Your Business Needs
To choose suitable costing procedures, businesses should consider their size, the type of products they make, and their market situation. Smaller businesses might prefer simpler methods, such as job costing, while larger operations could benefit from detailed systems like Activity-Based Costing. Production volume and variety significantly influence the choice of method. Market dynamics, such as pricing pressures and competition, also guide decision-making.
Benefits of Customized Costing Systems
Using customized product costing systems can give a business clear advantages. These systems address specific company needs, improve accuracy, and offer better control over costs. Customized costing helps businesses quickly adapt to changes, providing useful insights that standard methods might overlook. Tailoring cost estimation approaches to fit business goals ensures better decisions, higher efficiency, and improved financial results.
Common Mistakes in Product Costing and How to Avoid Them
Avoiding common errors in product costing systems can significantly improve your business outcomes.
Underestimating Indirect Costs
Indirect costs include expenses like utilities, equipment maintenance, and administrative salaries. Businesses often overlook these costs, leading to inaccurate pricing and reduced profits. To avoid this mistake, carefully identify and regularly review all indirect costs. Proper allocation ensures your pricing covers actual business expenses.
Inconsistent Cost Allocation
Using inconsistent methods to allocate costs can confuse financial records and mislead decision-makers. Clear and uniform costing procedures help businesses compare profitability across products and projects accurately. Implementing standard methods across your entire business promotes financial clarity and better strategic decisions.
Neglecting Regular Reviews
Businesses frequently make the error of not regularly reviewing their cost estimation approaches. Markets, materials, and labor costs change often, impacting overall costing accuracy. Regular reviews of costing methods keep your business prepared, competitive, and financially accurate. Consistent updates help you adjust quickly and maintain reliable financial data.
Frequently Asked Questions on Costing Methods and Approaches
Clear answers to common questions about costing methods and product costing systems help businesses better manage their operations.
What is the best costing method for small businesses?
Job costing or standard costing often suits small businesses. These methods are simple and effective for tracking specific projects or routine production.
How does inventory costing affect profitability?
Inventory costing influences the cost of goods sold and net profit. Using accurate methods like FIFO or weighted average helps manage inventory value and profitability clearly.
Can I switch costing methods during a financial year?
Changing costing approaches mid-year can be complex. It’s best to make changes at the start of a new financial year to avoid confusion.
Why is Activity-Based Costing considered accurate?
ABC closely tracks expenses tied to specific activities. It provides detailed and exact cost data, making it highly accurate.
What are the differences between FIFO and LIFO?
FIFO sells the oldest stock first, reflecting current prices clearly. LIFO sells newer stock first, which may lower profits and taxes during price inflation.
How frequently should costing systems be reviewed?
Regular reviews every quarter or at least annually help maintain accuracy and adapt to market changes.
Are digital ERP systems beneficial for cost management?
Digital ERP systems streamline product costing processes, improve accuracy, and provide real-time financial data, benefiting overall cost management.
What are the advantages of using marginal costing?
Marginal costing helps businesses clearly understand the impact of variable costs, aiding quick and accurate decisions on pricing and production levels.
Is weighted average costing suitable for all businesses?
Weighted average costing works well for businesses with similar inventory items. It provides simplicity and accuracy for inventory valuation.
How do costing methods impact pricing strategies?
Accurate costing helps businesses set competitive and profitable prices. Different costing methods influence how clearly businesses understand their actual production costs, affecting pricing strategies.
Read‑alikes
Understanding the Production System in Manufacturing: Types, Benefits, and Examples
Discrete Manufacturing: Key Elements, Insights, and Benefits
Piece Rate Pay — A Complete Guide for Employers & Workers
Understanding the Cost of Goods Manufactured: Formula, Components, Examples & Importance