McKinsey analyzed SMEs in 16 countries and found that MSMEs represent 90% of all businesses globally, account for ⅔ of business employment in advanced economies, and nearly ⅘ in emerging economies. According to the Indian Ministry of Micro, Small & Medium Enterprises, the share of MSMEs of India’s total manufacturing output equals 35.98% in 2020–2021. Moreover, the number of MSMEs in India is expected to grow from 6.3 crore (October 2023) to 7.5 crore. The competition in this market is high indeed. To increase one’s chances of success, we recommend digitizing business the sooner the better.
Every manufacturer, from the owner of a sewing workshop to the director of a furniture factory, has to deal with several tasks at the same time. They have to manage inventory, purchase raw materials, control the work of employees, and monitor the entire production cycle.
How to set up stock management & warehousing, and automate production? What to start planning tasks with? How to calculate profitability? How to manage production remotely? How to deal with scrap & by-products? Timur Amerkhanov, Product Manager at the Manufacturing Unit of Kladana, helped us find answers to these and other questions.
- Why is Production Management Important? Is it Possible to Do without it?
- How to Start Production Management?
- How to Plan Production Properly?
- How to Control Production?
- Why Count WIP (Work-in-Progress)?
- How to Deal with Scrap & By-Products?
- How to Calculate Production Profitability?
- What Are the Lean Manufacturing Principles?
- What Is the PDCA Cycle?
- Frequently Asked Questions on Production Management
💻 Free Webinar Recording Available!
Recently, we hosted the webinar Automation for Manufacturing Companies: Where to Begin, featuring Aleksandra Brovchuk, Kladana’s Director in India, and Uday Sharma, Senior Customer Support Executive.
They shared the insights on efficiently managing inventory, warehousing, sales, and production — all within a single app, without requiring expensive implementations or specialized skills.
Key topics covered included:
- 6 common production management challenges and solutions
- 5 steps to seamlessly implement manufacturing software
- How Kladana ERP can benefit manufacturing companies
Receive webinar recording, presentation slides, a promo code for an extended 30‑day trial, and additional content via email for free.
Why is Production Management Important? Is it Possible to Do without it?
Production planning and control allows you to:
- Understand what tasks different departments of a manufacturing company are working on and how they interact with each other.
- Assess whether there are enough raw materials in stock and whether human resources are sufficient for all production operations.
- Synchronize supply with the current and future production orders by using demand forecasting.
- Calculate labour & operation costs together with the unit cost. Thus, it’s easier to manage pricing.
To correlate upcoming costs with expected profits, you need to record all production processes.
It is easier to avoid mistakes and reduce WIP if you plan all production stages in the same software where you manage inventory. Kladana is just such a solution.
In Kladana ERP, you can keep records at every stage of production. This includes recording the receiving of raw materials, moving products between warehouses, and conducting inventory countings. You can also manage stock in a warehouse, reduce storage costs, assign tasks to employees, and calculate the unit cost of finished goods in order to distribute financial flows and increase the profitability of a manufacturing company.
Use a free 14‑day trial to decide whether our software suits you. No credit card required.
Before Kladana, we were doing everything in Excel. All the stock and production records were maintained in spreadsheets. We weren’t able to arrange timely updates for the information about warehouse stocks: the materials we were receiving, the goods we were shipping.
It was hard for us to acknowledge which products we had in abundance and which we lacked. Some wrong decisions and production delays followed.
How to Start Production Management?
Businesses have different approaches to managing production. Manufacturing companies with one workshop and a small number of employees sometimes use spreadsheets. This approach works for some time until the company expands. As soon as new warehouses, facilities, product range and employees are added, the spreadsheets are no longer useful. They lead to multiple mistakes and long hours of tedious work.
Complications arise, but people keep production records in Excel filling in endless tables manually. Someone makes compound macros and tries to automate everything, but it is inconvenient because Excel has no database. As soon as streaming production begins, this scheme breaks down: employee A erases a formula, B — does not update the price information on time, and C — copies data from the wrong cell.
In manufacturing, It is easier to organize warehousing and stock management in cloud-based software that combines the receiving of raw materials and shipment of finished products, as well as the data on the counterparties and stock on hand.
Read-alikes
Top 23 Manufacturing Management Software
Full Guide to MRP Solutions: Core Features, Advantages and Pitfalls
How to Plan Production Properly?
First, you need to prioritize the execution of orders. When the manufacturing company’s managers understand exactly what needs to be produced and in what quantity, they can make a BOM (Bill of Materials). This document describes the entire flow of manufacturing a product, including all the necessary components.
During the planning of manufacturing clothing, shoes, cars, motorcycles, tires, pharmaceutical products, and other goods, you need to pay attention to:
- quantity of raw materials;
- supply of resources;
- number of working shifts and employees;
- equipment utilization.
Kladana has a form for production planning — it’s called a production order. It is also used to control the completion of the order. A production order can be created as part of a sales order. Or you can schedule it to plan work for a week or a shift.
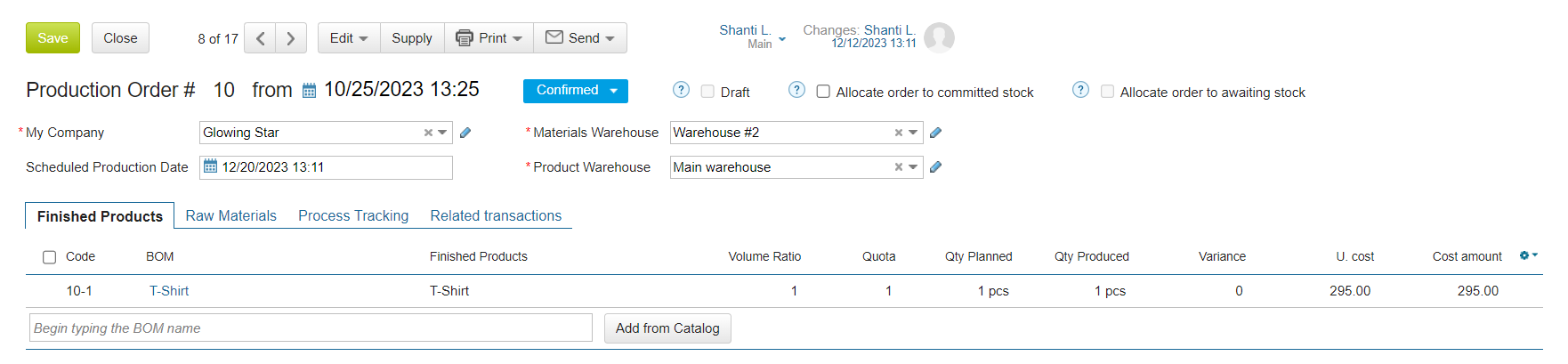
The first stage is to determine what we need to produce. The second step is to determine the necessary resources. For this purpose, there is a tab with raw materials in the production order. And to keep track of the completion of production operations, you need to look at operation reports. Kladana allows you to record all the processes not only in the warehouse but also in the production workshop. And it is not difficult to do it. The user ticks a checkbox, and all the raw materials for that stage of production are written off there.
How to Control Production?
When everything is planned and stock management is in place, the manufacturer understands how long it will take to complete production orders and can divide the entire process into steps. As each step is completed, it’s important to write off the raw materials that were used on time — for example, fabric and thread for clothing or wood and hardware for furniture. In Kladana, raw materials are written off automatically. If a production cycle lasts a week and the employee marks the completion of each stage at the end of the shift, you can tell exactly what goods are currently in stock.
Read-alikes
Artisanté: How to Streamline Chocolate & Coffee Manufacturing Management in Half a Year
Unicorn Natural Products Manufacturing: a Journey from Spreadsheets to ERP
Cura Pharmaceuticals Manufacturing: Increased Data Accuracy & Business Workflows in 6 Months
If you do not control what exactly happens at a particular stage, then production reminds one of a «black box». This happens when the head of the enterprise sees only the final report on how many raw materials were written off and how many finished products ended up in the warehouse, but they do not know whether there was an overconsumption of raw materials and whether scrap and by-products were recorded.
Kladana allows you to open the «black box» and see what really happens there. In essence, it is a task manager, which also writes off raw materials and shows the unit cost of finished products. For the process tracking, you divide a production order into several operations, and mark each stage completion sequentially. The only thing you need to do in advance is to create BOMs. Specify what materials and at what stage are used, and then everything will be automatically written off during production. This is convenient, since usually the composition of products does not change much.
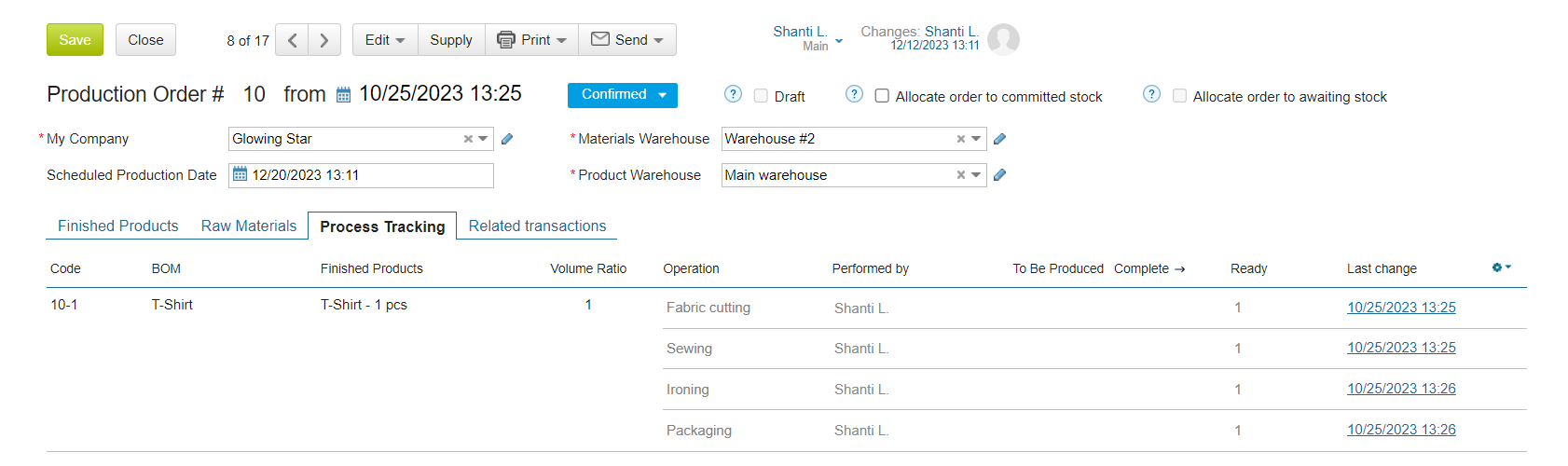
Here’s how you need to build your manufacturing workflow to make it easier to control production operations completion in Kladana or another software:
1️⃣ Set up a workflow to understand how many stages of production you’ll have. For garment production, typical operations are cutting, sewing, quality control (QC), and packaging.
2️⃣ Create a BOM for a product you are going to produce. Describe the model and size of a shirt, specify that at the cutting stage, it will take 20 m of fabric, at the sewing stage — 10 buttons or one zipper and fastener, and for packaging you will need a special bag and a label.
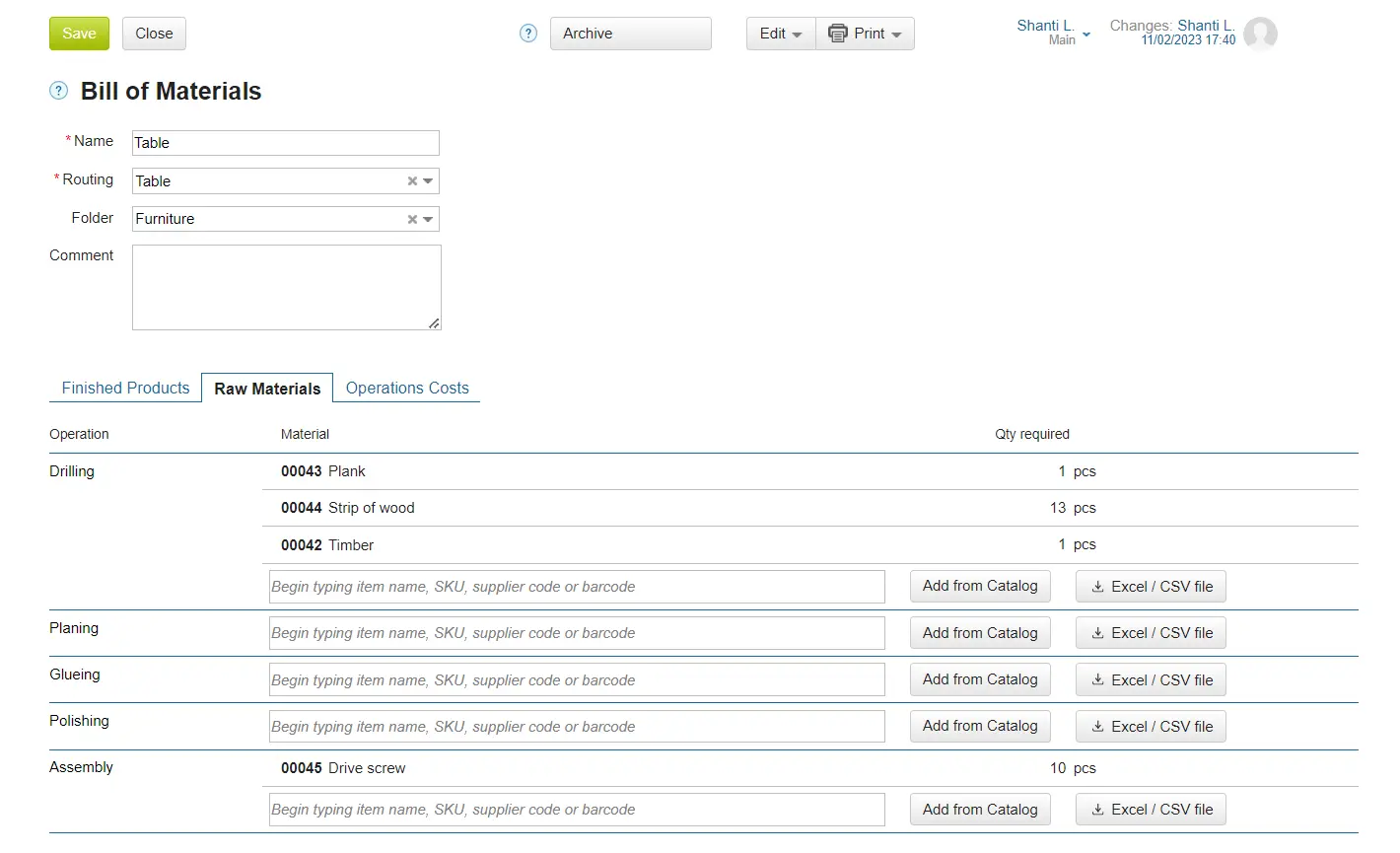
3️⃣ Add a BOM to a production order. You can specify that you have, for instance, an order for five shirts, 10 dresses, and 15 pants. The final number can go up to 100, especially if it’s food manufacturing.
4️⃣ Mark the completion of production operations to automatically write off raw materials. As soon as all the stages are completed, the finished product is transferred to the warehouse and the unit cost is calculated for it. At this point, the price will be more accurate than during the planning period. During the production process, you can control the unit cost for one specific item or several items.
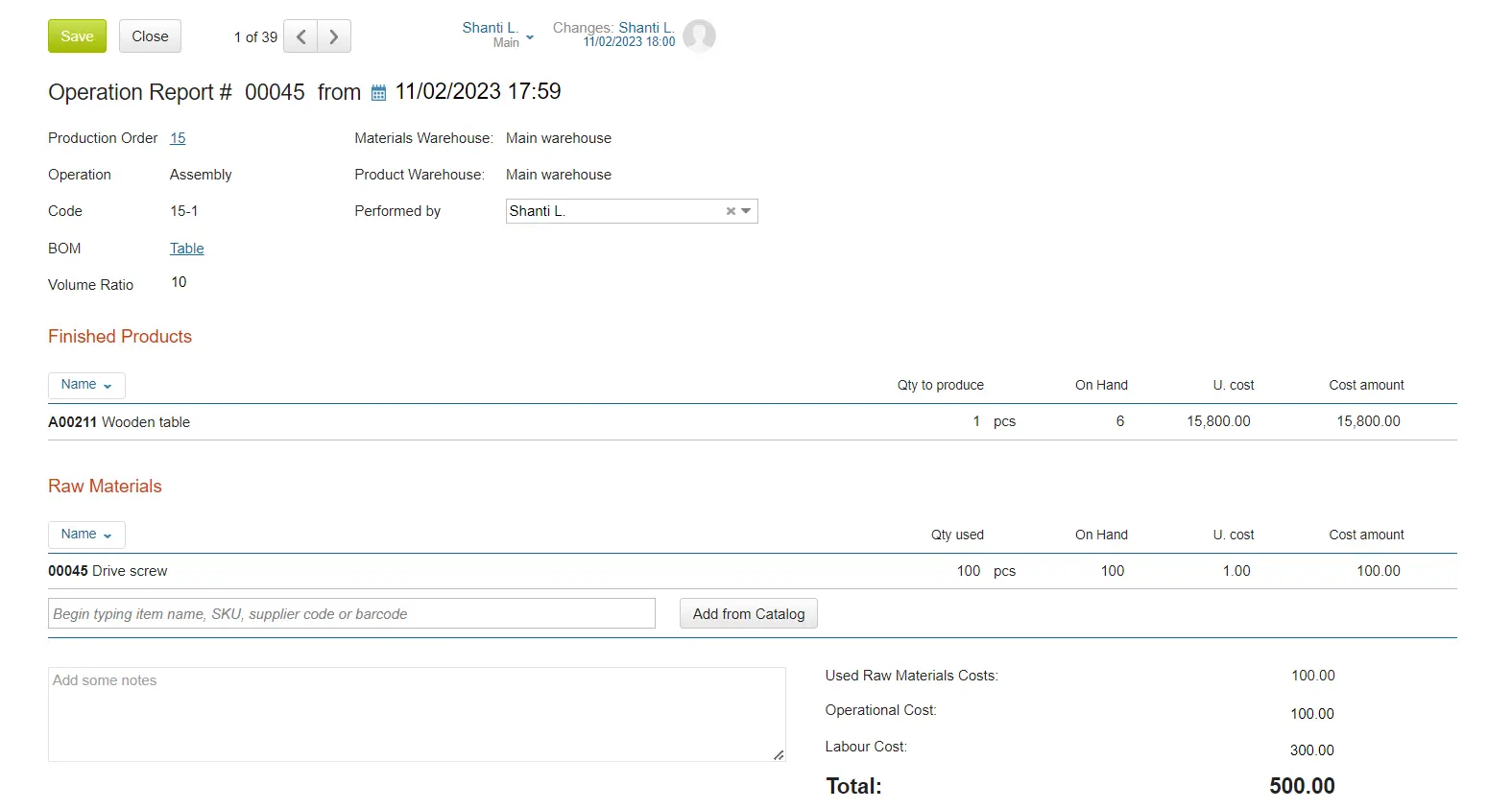
Even before all the production operations are completed, the manager can open the production order, assess how much has already been done, and estimate when the order will be done. If at any stage the work has stopped, it is immediately visible, and immediate actions can be taken.
Handy Tip
Learn more about creating BOMs, production orders, production reports, and other manufacturing management features in Kladana.
Why Count WIP (Work‑in‑Progress)?
Sometimes businesses keep blanks for future products in order to speed up work when they receive a new order. For example, a sewing workshop cuts fabric for dresses, so that the equipment does not stand idle, and employees do the work and get their fees. If a manufacturing company receives an order for pants or other items made from the same fabric, some problems arise.
There is a risk of overstocking when a company sends such blanks to a warehouse. The blanks take up storage space, and money is spent on them. All this leads to an increase in work-in-progress. It must be taken under control.
If you plan the steps and control their execution, you need to understand when exactly WIP occurs and how to calculate it. You can estimate the amount of work-in-progress and reduce it with Kladana. Go to the Stock report and assess the number of WIP in the column called In Transit. This will reduce production costs and increase profitability.
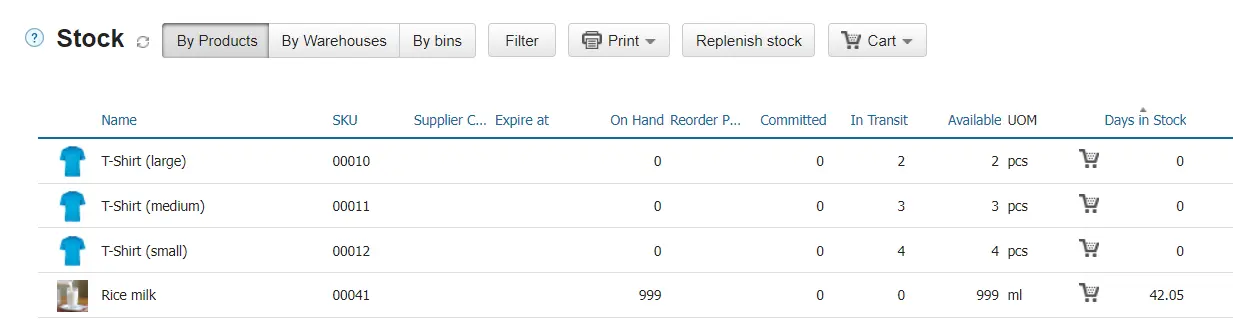
Counting WIP can be done on its own. The easiest way is to conduct inventory counting and compare the results with the documents that confirm the production of finished products. Then one needs to determine the cause of other direct costs and take for this purpose the fixed percentage of the cost of raw materials. It will turn out that the volume of WIP is equal to the price for raw materials together with other direct costs.
In order to count WIP at the cost of raw materials, you need data on stock. Knowing this, you can move on to the price of unfinished goods.
How to Deal with Scrap & By‑Products?
Even the most careful planning doesn’t always help you avoid scrap. For example, culinary products can be burned because of equipment failure, and fabric patterns will turn out to be unsuitable because of an employee’s mistake. Divergences that occur at any stage of production need to be taken into account, as they affect the unit cost.
Say, you expected to earn 20% but in fact, you earned 10% because your staff ruined the fabric. In clothing, fabric is a major cost item. In Kladana, you can specify the quantity of actually used fabric — for instance, 20 meters instead of 10. The opposite situation may happen when you use scraps from the warehouse and sew them together. In this case, 5 meters of fabric is actually used.
Production orders help to understand the reason why the company spends more resources to complete orders than originally planned.Thus you can see at what stage a scrap occurred and which employee was responsible for it.
To correct the situation after a scrap occurs, the company often raises the price of the finished product. Sometimes this leads to a decrease of consumer demand. One solution to such a problem may be to reconsider what exactly is worth producing.
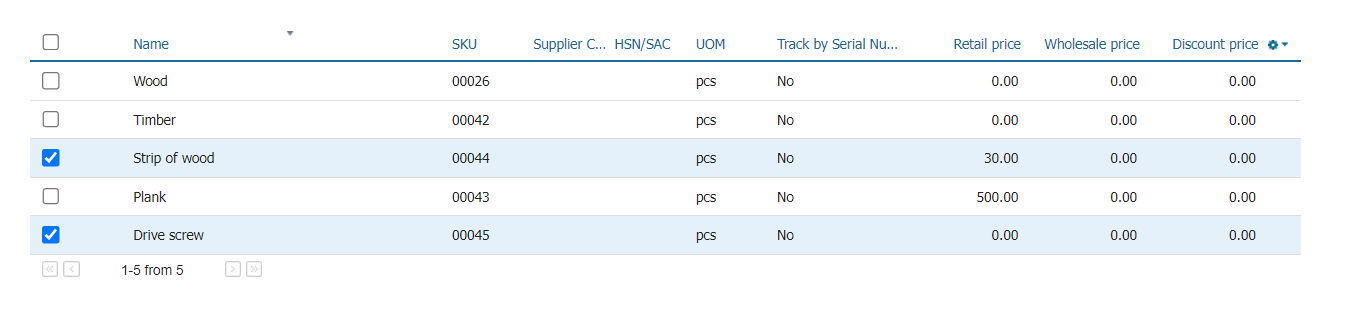
How to Calculate Production Profitability?
Estimating how much a company will earn after the production order is completed should be done during planning. To get the expected profit, it is necessary to correlate the selling price with the projected cost of materials.
As a result of the completion of all stages, finished products appear. The calculation of the unit cost is made up of the number of costs that are directly or indirectly related to the manufacturing process, including labour & operational costs.
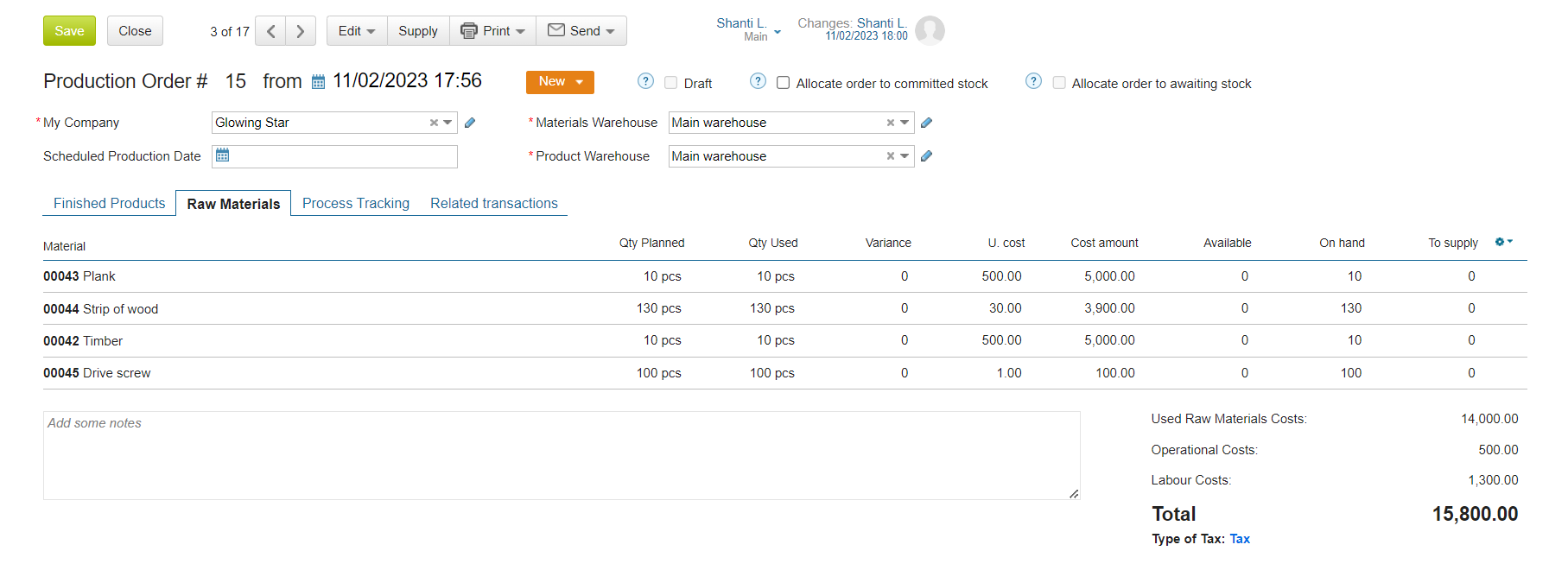
The enterprise sells goods and records the revenue, from which it then subtracts the cost of production. So it turns out to calculate profitability. According to it, you can draw conclusions about the effectiveness of the work done.
You can calculate the unit cost on your own by using the following formula:
(Direct costs + indirect costs) / number of produced items
Don’t forget to take scrap into account.
In Kladana, you can use the automatic Profit report which simultaneously shows the profit from the sale of goods for a given period of time and the profitability of individual products.
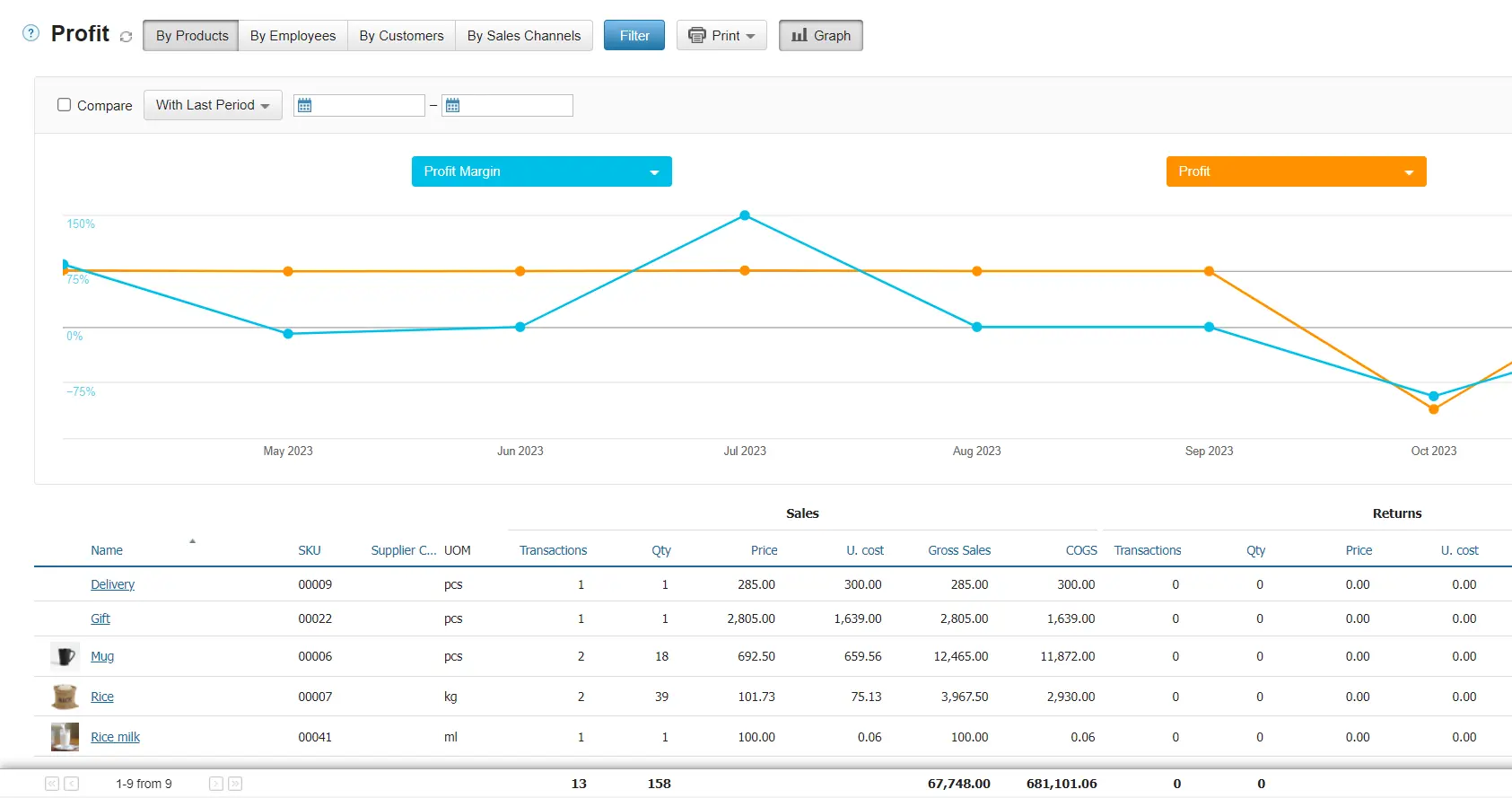
When you produce everything you have planned, you can generate a report to understand which items we should produce more and from which we’d better refuse. There are two important indicators: speed and profitability. For example, you can produce a lot of goods but have low profitability, or vice versa. In any case, it is important to find a balance and then to make management decisions.
Calculating and monitoring production costs is particularly important in the food industry. Enterprises in this sector are usually low-margin, and their profitability is low. Even at the planning stage, you need to understand how many products are required and when they will be delivered. This is due to their limited shelf life. If the goods expire before they are sold, they will have to be written off, which is already a loss.
What Are the Lean Manufacturing Principles?
Lean production pursues a few goals:
- To reasonably reduce resources
- To increase customer satisfaction
- To improve productivity in general
Five core principles of lean manufacturing are acknowledged:
Value
To identify the value of an item or a service, an entrepreneur must assess it from a customer perspective. The outcome of this stage should be creating or improving products that meet the demands of the target audience.
Value Stream
To map the value stream one must define the entire cycle of creating a product, including all production stages, design, etc.
Flow
In creating a production flow working like clockwork, an entrepreneur must take into account all aspects, including raw materials purchasing, manufacturing, employee workload, shipment, etc. The goal of this stage is to reduce scrap and to decrease time spent on the flow.
Pull
A push production scheme is a traditional one that is based on forecasting and sometimes leads to overstocking and large amounts of WIP. In contrast to that, a pull-based production system focuses on customer demand, and new production orders are created out of sales orders.
Perfection
This principle is based on the thought that no production system can be perfect enough, and an entrepreneur should always seek new ways to improve it.
What Is the PDCA Cycle?
PDCA (plan—do—check—act) is a rather simple scheme used in problem-solving in production routines.
- Plan — one has to determine the possible problem, the desired outcome, and the steps one needs to take in order to solve the problem.
- Do — one implements a plan step by step and makes amendments if something goes wrong.
- Check — one revises how well the plan was implemented and whether this test was a success.
- Act — one has to decide whether to implement the change on a larger scale or take a step back, correct all mistakes, and repeat PDCA once again.
Frequently Asked Questions on Production Management
Discover the answers to common questions people have about manufacturing management.
What do you mean by production management?
Production management is the practice of organizing, planning, directing, and controlling all the activities that lead to the production of goods or services, aiming to produce high‑quality products efficiently and cost‑effectively.
What is the objection of production management?
The main objective of production management is to ensure that goods and services are produced efficiently, meeting the quality standards demanded by customers, at the lowest possible cost, and delivered on time.
What are the 3 main functions of production management?
- Planning: Deciding on the production process and determining the resources required;
- Organizing: Coordinating materials, equipment, and labor to implement the plan;
- Controlling: Monitoring production to ensure it stays on schedule and meets quality standards.
What is the process of production management?
The process of production management involves setting production goals, planning and scheduling production activities, implementing the production plan, monitoring the production process to ensure efficiency, and making adjustments as needed to meet production targets.
What are the basic types of production control?
- Job shop production: Customized production based on specific customer orders;
- Batch production: Producing a limited number of identical products in a batch;
- Mass production: Continuous production of large quantities of standardized products;
- Just‑in‑time production: Producing goods only as they are needed to minimize inventory costs.
What are the 5 steps in production control?
- Planning: Determining what to produce, how much to produce, and the production method;
- Routing: Deciding the flow of work, from start to finish;
- Scheduling: Timing the tasks for optimal production efficiency;
- Dispatching: Assigning work to different machines or workstations;
- Monitoring and controlling: Ensuring production meets the planned schedules and standards.
What are the 5 principles of lean manufacturing?
- Identify value from the customer’s perspective;
- Map the value stream to identify and eliminate waste;
- Create a continuous workflow that allows for smoother production;
- Establish a pull system that responds to customer demand;
- Pursue perfection by continuously improving processes and eliminating waste.
What is the PDCA cycle process?
The PDCA (Plan‑Do‑Check‑Act) cycle is a four‑step management method used for the control and continuous improvement of processes and products. It involves planning an action, implementing the plan, checking the results to see if the desired outcomes were achieved, and acting to make improvements before the cycle starts again.