Warehouse bin storage is an organizational method where each storage spot is assigned an address or unique number, creating a warehouse topology.
A well-structured bin system speeds up order assembly, shipping, and goods receiving by helping staff locate products faster and with less confusion. It also reduces picking and placement errors, minimizes delays, and supports more accurate inventory tracking.
Here’s how to implement this system and maintain efficient warehouse management.
- What is Bin Storage?
- Who Benefits from Warehouse Bin Storage?
- Why Bin Storage is Essential in Warehousing for SMEs: Key Benefits
- Types of Bin Storage Systems
- Cell-Based Storage
- Principles of Operation: How Bin Storage Works in a Warehouse
- Solutions for Small Warehouses
- Implementing the Bin Storage System: A Step-by-Step Guide
- Best Practices for Bin Location Management
- Final Thoughts
- Frequently Asked Questions on Warehouse Bin System
- List of Resources
What is Bin Storage?
Bin storage simplifies the search for necessary items in a warehouse and speeds up sales order collection. It optimizes operations and minimizes human errors. Without an organized system, warehouses can face delays in order fulfillment and product spoilage.
In a warehouse bin management system, the warehouse is divided into sections or locations, each assigned an exact address. Every bin has its own code, so each incoming batch, item, or group of items is stored at its designated address.
Who Benefits from Warehouse Bin Storage?
The warehouse bin system is ideal for companies with a wide product range or those dealing with perishable goods, like food products. A well-structured logistics system within the warehouse is crucial.
The statistics speak for themselves: according to Verified Market Reports, the global market for storage bins and totes is on the rise, driven by the growing demand for better space organization in both businesses and households. Valued at USD 12.75 billion in 2024, the market is expected to grow steadily and reach USD 18.5 billion by 2033.
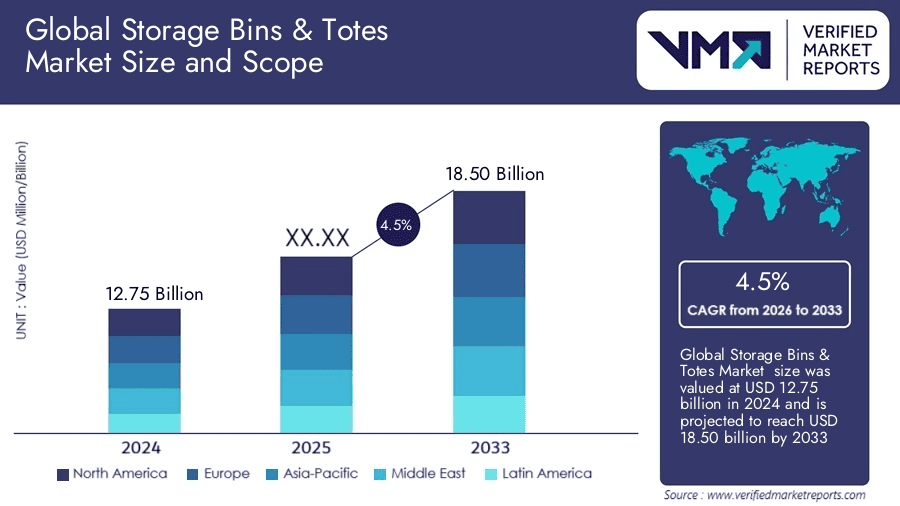
Implementing storage bins can significantly enhance operational efficiency and order accuracy, ultimately leading to better customer satisfaction and streamlined warehouse processes.
Why Bin Storage is Essential in Warehousing for SMEs: Key Benefits
- Enhanced Efficiency: Warehouse workers always know the exact location and quantity of products on hand or committed, allowing for quicker receiving and picking of goods.
- Improved Navigation: Clearly marked and named locations and cells help staff easily find items for collecting sales orders.
- Simplified Inventory Management: Each product has a unique address, making it easy to locate, which significantly simplifies inventory counts.
- Better Orientation: Storage rules help employees quickly orient themselves in the warehouse during receiving and order picking.
- Accurate Data: Provides precise data on the availability and location of each item. This enables more accurate inventory planning, optimized ordering, and avoids entries duplication.
- Reduced Write-offs: Allows control over product expiration dates, reducing losses.
Bin storage provides accurate data on the availability and location of each item, allowing for more precise inventory planning, optimized ordering, and avoidance of duplicate entries. It also enables control over product expiration dates, reducing write-offs. Products can be organized into locations and bins based on their characteristics, storage conditions, or sizes.
For example, locations and bins can be associated with specific brands or manufacturers, product sizes (like potted flowers, shrubs, or plant seeds), or categories like raw materials, finished goods, and items returned from marketplaces.
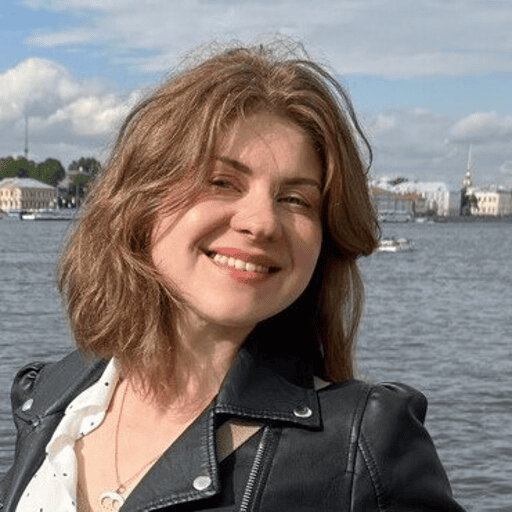
Types of Bin Storage Systems
Depending on a company’s operations and warehouse specifics, one of two storage systems can be used: dynamic or static bin storage.
Static System
In a static system, each product group is assigned to a specific warehouse area with a fixed number of bins designed to accommodate the maximum possible delivery volume.
This setup is suitable for warehouses storing finished goods for companies with a stable product range.
Dynamic System
In a dynamic system, storage locations are not assigned to specific product groups. Instead, items are assigned a unique identifier and placed in any available bin. The warehouse may still be divided into zones for different product types, but within each zone, products are stored in any free space.
The dynamic system is considered more advanced and allows for more efficient use of warehouse space.
Comparison of Storage Systems
Both systems have their advantages and disadvantages. For convenience, they are summarized in the table below.
Criteria | Static | Dynamic |
Pros |
Increased transparency and logical flow of processes. Simplified product search and easy order picking. Reduced training and adaptation costs for new staff. |
No wasted space for specific product types. Reduced time for receiving and placing goods. Efficient use of warehouse space. Time and labor savings for assortment analysis. |
Cons |
Idle slots when products are unavailable. Requires regular assortment analysis. Complex process of product placement. |
Challenging implementation: requires more sophisticated infrastructure and software, as the warehouse needs to be automated. |
Summary:
- A dynamic system is more efficient for large warehouses with a constantly changing assortment.
- A static system works best for warehouses with a limited, stable product range.
Cell-Based Storage
In cell-based storage, the warehouse is divided into compartments (cells) of specific sizes. Products are placed in them according to their dimensions and characteristics.
In bin-based storage, each product is assigned a unique location code, which simplifies product search and picking. If needed, a specific item can be located quickly. In cell-based storage, products are grouped by cells, and a dedicated indexing system or bin map is required for efficient searching.
📍 Trying to master warehouse inventory management from scratch? Read our guide to learn the fundamentals: Warehouse Inventory Management: a Complete Guide to Tools, Tips and Systems for 2025
Principles of Operation: How Bin Storage Works in a Warehouse
To begin, you need to decide which system of storage will be used. After that, the process follows several steps.
Defining Warehouse Zones
The warehouse should be divided into at least three main areas:
- Receiving zone — This is where goods first arrive. Here, they are checked against the supplier’s documentation and labeled.
- Storage zone — This is the part of the warehouse where goods are moved for storage.
- Shipping zone — This is where goods are taken during order picking. Packing lists are created, documentation is printed, and orders are dispatched to customers.
Each of these zones can be further divided into subzones. For example, the storage zone can include:
- Pallet storage subzone — Handled with special equipment like stackers and forklifts.
- Small-item subzone — Orders are picked manually here.
- Special storage condition subzones — For example, cold storage, fragile item sections, etc.
These divisions help avoid, for instance, sending a stacker into a narrow aisle for small items, or storing food products next to household chemicals.
💡 Tip: In addition to the required zones, optional ones can be created, such as a rejection zone for storing damaged or non-compliant goods.
Preparing the Bins
Each subzone is further divided into bins: shelves, levels, racks, and individual positions. Every element is assigned a unique number.
For example, a bin can be identified using: row, position, level, cell. Each element has its own identifier, and when combined, they create a unique address for the product location.
Before organizing zones or bins, carefully plan their layout for convenient and fast access to products — based on your specific warehouse processes and employee workflow. For example, raw materials should be closer to the production area. Returned goods from marketplaces should be near the receiving or return processing zone. Finished goods or top-selling brands should be closer to the packing or shipping zone, while rarely ordered products can be placed deeper in the warehouse.
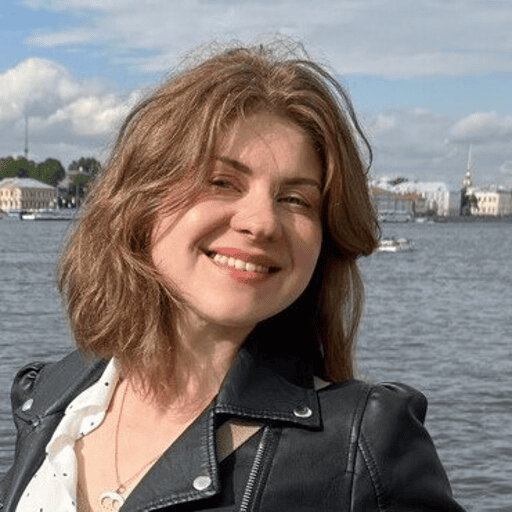
Coding System
If there are multiple warehouses, it’s best to assign them letters. For individual bins, use numbers. Separators like dashes, dots, or colons can be added to create a clear format.
Example: A warehouse bin address might look like B13-06-04, where:
- B — warehouse zone
- 13 — rack number
- 06 — level
- 04 — bin/cell
For floor storage systems, the address might look like B-25, where B is the row, and 25 is the position within it.
A few non-obvious coding rules:
- Avoid using color labels — they add unnecessary complexity.
- If you use similar colors, it may lead to confusion and picking errors.
Implementing Software and Purchasing Equipment
To implement bin-based storage and manage an addressable warehouse, you’ll need:
- Label printer — for printing bin address stickers with barcodes
- Barcode scanner — preferably wireless for mobility
- Computer and inventory management system — such as Kladana
- Thermal transfer printer — prints durable labels that resist abrasion, moisture, and sunlight
- Mobile data terminal (MDT) — used to scan bin barcodes; requires installation of warehouse address storage software
The warehouse must have a stable wireless internet connection. This determines whether the MDT should support offline mode.
If internet access is unstable, set up a dedicated workstation where employees can manually verify goods after picking — either using a packing list or an MDT in offline mode.
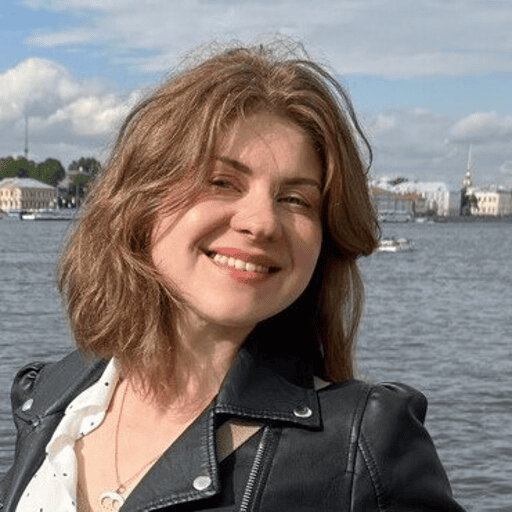
Staff Training
Each employee must clearly understand the sequence of their responsibilities. In a bin storage system, their work becomes easier and consists mostly of simple, mechanical steps.
Staff should also be trained to operate warehouse equipment and use the required devices.
Test Run
Before full implementation, it’s best to conduct system testing. Any potential mistakes or incorrect workflows should be identified and eliminated early.
💡 Tip: Use a few slow-moving items or products from a “small client.” This way, you can easily reset inventory records later if needed and test the system with minimal risk.
Solutions for Small Warehouses
Bin storage is primarily suited for large companies with thousands of SKUs. In small warehouses (up to 300–500 sq. m), this system may actually complicate operations. However, that doesn’t mean automation isn’t needed.
Our client with a small warehouse is implementing a bin storage system to maximize the use of available width and height.
They use a dynamic storage system, which helps avoid losing track of products stored in small quantities — for example, on the upper shelves — because the system shows exactly where the product is located.
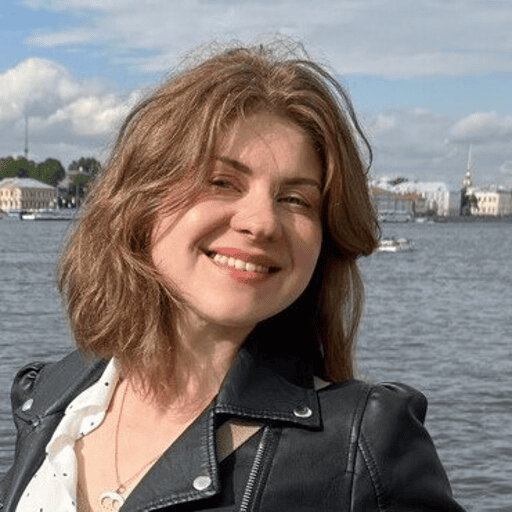
Products with Limited Shelf Life
Items with expiration dates require a more flexible storage approach. It’s essential to label incoming goods and record their production dates in the system. While this may take extra time, it significantly reduces losses from expired stock.
You can also implement bin storage by assigning each product to a specific bin. This enables grouping of goods by expiration date in the same zone. The system will then guide pickers to the correct location.
Products with Unlimited Shelf Life
If the products don’t expire and the owner doesn’t care about the order in which goods are shipped, bin storage can make product searches more complicated. In such cases, it’s more important to control incoming and outgoing stock, which is where bin labeling becomes essential.
With a dynamic system, different products may be stored on the same shelf or even in the same bin to save space.
That’s why a proper inventory system is crucial — it helps identify the exact location of each item.
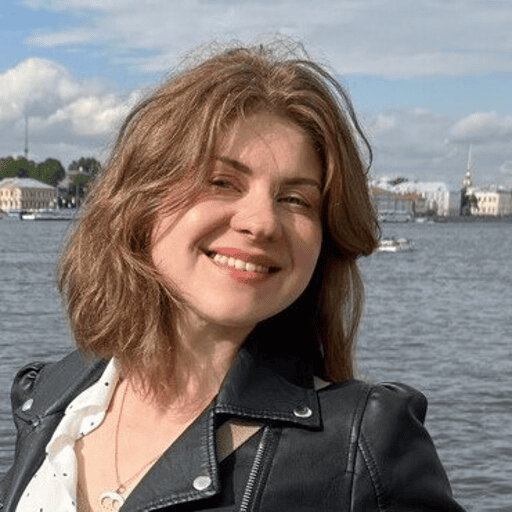
Implementing the Bin Storage System: A Step-by-Step Guide
The adoption of WMS is on the rise. According to Grand View Research the global warehouse automation market was valued at $19.23 billion in 2023 and is expected to grow to $59.52 billion by 2030, with an average annual growth rate of 18.7% between 2024 and 2030.
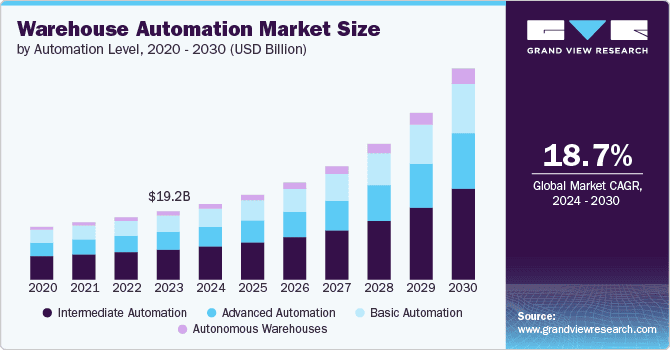
Using Kladana ERP as an example, we will break down the process of implementing a bin storage system supported by efficient software.
Step 1: Analyze Warehouse Operations and Product Specifications
Consider the number of SKUs and product groups, product dimensions, weight characteristics (since not all goods can be stored on the upper levels), and shelf lives.
This information helps determine the required floor area and the number of storage locations. It directly influences the warehouse’s topology.
Step 2: Assign Addresses and Label Shelves
Every component of the warehouse — row, location, level, and bin — should have its own number. Combined, they create a unique address for the product’s storage location.
Step 3: Define Zones and Bins
Kladana allows you to create one or multiple warehouses, each managed separately.
- The warehouse is divided into storage locations. You can create up to 10 locations per warehouse.
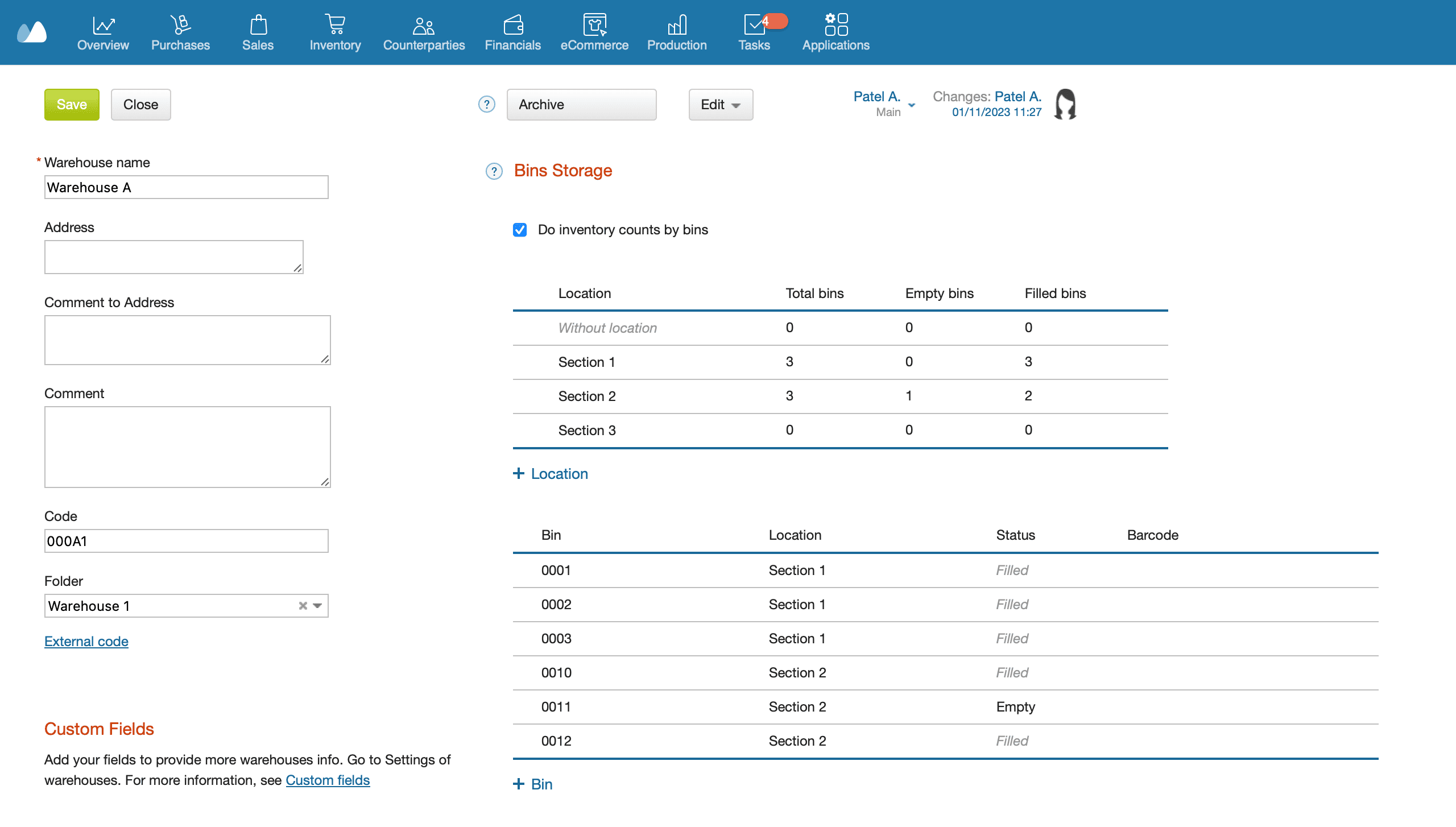
- Next, add bins, name them, and assign them to the appropriate locations.
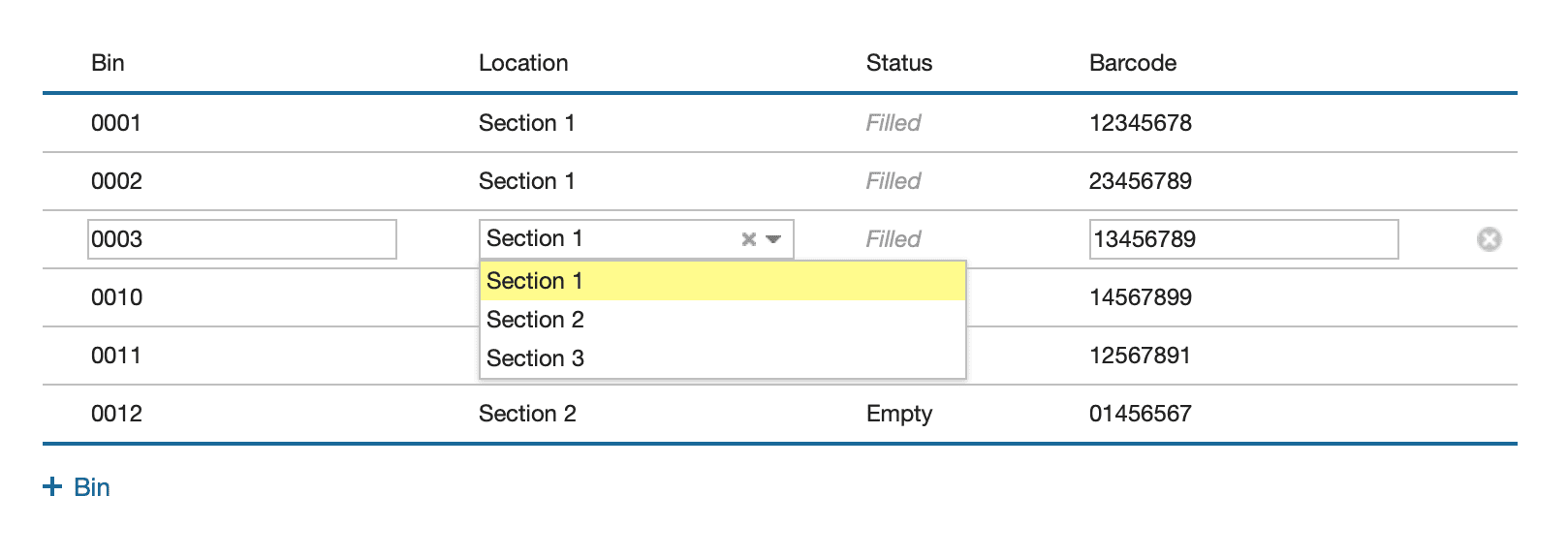
- If a warehouse is no longer in use, it can be archived. Its data will be hidden yet remain in the system, with the option to restore and resume operations at any time.
Step 4: Order Assembly and Pick List Printing
Goods receiving and dropping of items on stock records occur with just a few clicks. Simply select the warehouse, choose the appropriate bin (s), and pick the product (s).
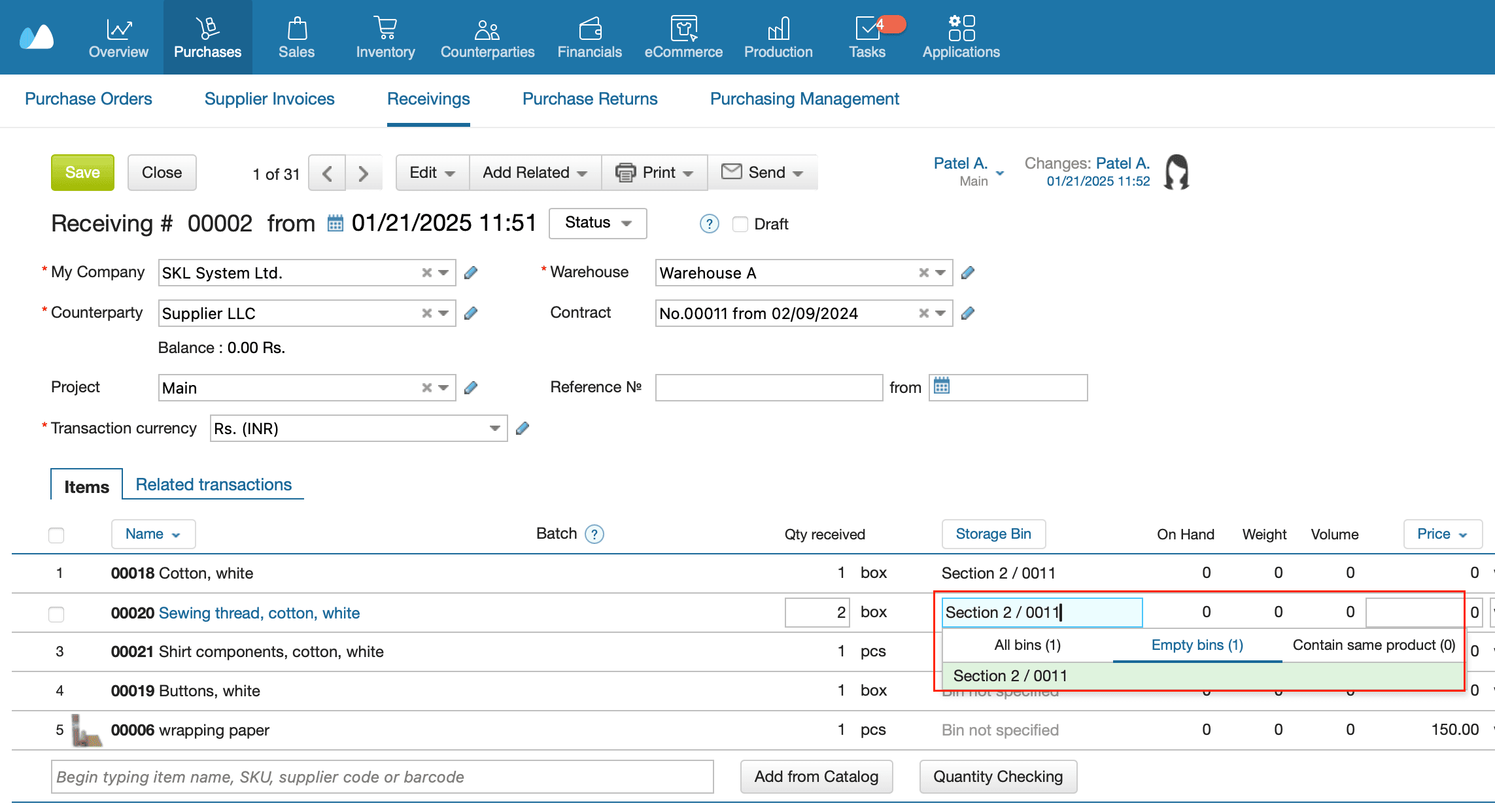
- Bins for shipping can be selected automatically or chosen manually.
- Errors are minimized: if there are products without a designated storage bin, a notification appears on the screen. However, the system does not prevent you from saving documents without specifying a bin.
- For additional convenience during order assembly, a pick list can be printed. This list details the zone and bin from which the products were shipped.
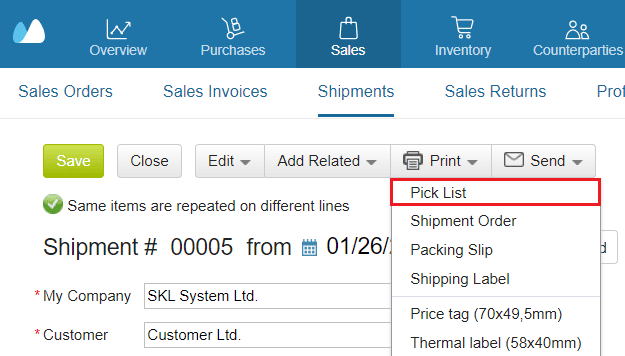
- Remaining stock can be reviewed in a dedicated report — allowing you to verify product data and identify the bins in which they are stored.
📍 Boost your warehouse efficiency — learn about smart barcoding: Revolutionizing WMS Efficiency: Smart Warehouse Barcoding
Best Practices for Bin Location Management
A well-managed bin system saves time, reduces picking errors, and supports smoother inventory operations.
✅ Assign SKUs by velocity or product type
Store fast-moving items closer to the packing zone. Group similar SKUs or categories together to streamline picking and reduce walking time.
✅ Use clear, consistent labeling
Each bin should have a unique, readable code. Stick to one format (e.g., Row-Level-Bin), and avoid overcomplicating with long or inconsistent identifiers.
✅ Keep similar items separated to avoid picking errors
Avoid placing similar-looking SKUs side by side. It reduces the chance of picking mistakes, especially during peak hours or when onboarding new staff.
✅ Use color-coded zones or shelves
Color-coded shelving or zone signs help staff visually orient themselves and speed up navigation — especially useful in large or multi-level warehouses.
✅ Regular audits and real-time updates
Schedule bin checks and reconcile with digital records. Use your inventory!! software to reflect real-time stock movement and prevent bin mismatches.
📦 Bin-based storage & multi-warehouse support
Organize inventory using unique bin IDs across multiple warehouses for fast, accurate item location. Try Kladana.
Final Thoughts
Even small warehouses can benefit from a bin system. It brings structure, saves time, and prevents loss of stock.
A bin-based approach is often the first step toward full warehouse automation. With clear labeling and digital tracking, businesses lay the foundation for barcode scanning, inventory reports, and smarter replenishment.
Kladana ERP helps you implement bin storage quickly — with flexible configuration and responsive support to walk you through each step.
Customer Story: Neytthomes used to manage inventory in Excel but switched to Kladana for better control.
- Now they can see stock levels in real time across 10 warehouses.
- They added barcodes to 270 products and finished a full stock check in under an hour.
- Opening a new store and setting up inventory now takes just 30 minutes.
- Kladana helped them save time and avoid mistakes.
Frequently Asked Questions on Warehouse Bin System
Here are answers to the most common questions about bin storage systems in warehouses — especially for growing businesses looking to organize inventory better.
What is the purpose of bin locations in a warehouse?
Bin locations help you track exactly where each product is stored. They make inventory more organized, reduce search time, and simplify stock audits.
Do I need barcodes to use a bin location system?
No, but barcodes make the process faster and more accurate. You can start with manual labeling and upgrade to barcodes later.
Can small businesses use bin systems without WMS?
Yes. Even without a full WMS, businesses can use Excel or simple inventory software to assign and track bin codes.
How do bin locations improve warehouse picking?
They reduce search time. Pickers know exactly where to go, reducing walking distance and human error during order assembly.
How do I name or code my warehouse bins?
Use a consistent format like Zone-Rack-Level-Bin (e.g., A-05-02-03). Include only what’s needed, and keep codes short and easy to read.
What’s the difference between bin, rack, and shelf?
- Rack: A large structure with multiple levels
- Shelf: A flat surface within a rack
- Bin: The specific compartment or position where an item is stored
What’s the difference between static and dynamic bin systems?
Static bins are assigned permanently to specific SKUs. Dynamic bins change based on what’s available — ideal for high SKU turnover and limited space.
How many zones should I create in a small warehouse?
Three basic zones are enough: receiving, storage, and shipping. You can add special zones for returns, fragile goods, or cold storage if needed.
Do I need to re-label bins during stock changes?
Not if you use a dynamic system. You only update the system with new product-bin assignments. But labels should stay readable and accurate.
How does Kladana support bin management?
Kladana allows you to create storage zones, assign bins, track item locations, and print picking lists — all from one interface. You can also archive inactive warehouses without losing data.
List of Resources
- Verified Market Reports — Global Storage Bins & Totes Market Size And Forecast
- Grand View Research — Warehouse Automation Market Size, Share & Trends Analysis Report 2024 — 2030