Effective inventory management plays a crucial role in the smooth operation of companies both big and small. However, even the most seasoned businesses can stumble upon pitfalls that affect their inventory control.
Financial losses, eroded customer trust, ruined relationships with suppliers, full shelves with expired perishable goods, lack of motivation among the employees, and neglect of their duties, are typical consequences of bad decision-making in the sphere of inventory management.
In this article, we’ll delve into the common mistakes and issues that plague inventory management systems. Join us as we explore the challenges businesses face and uncover practical solutions to enhance their inventory management strategies.
- What is good inventory management
- How Inventory Management Mistakes May Harm a Company
- Overstocking
- Understocking
- Poor Inventory Visibility
- Unsuitable Inventory Storage
- Prevalence of Manual Processes
- Lack of Communication and Limited Skills
- Inadequate Integration with Other Systems
- Growing Competition
- Fluctuating Customer Demand
- Supply Chain Complexity
- Solutions that Automate Processes and Help Avoid Mistakes
- Frequently Asked Questions on Typical Inventory Management Mistakes
What Is Good Inventory Management
Good inventory management is crucial for the smooth operation of any business. It involves maintaining an optimal balance between supply and demand to ensure that products are readily available without excess stock. Effective inventory management prevents overstocking, which ties up valuable resources, and understocking, which can lead to missed sales opportunities.
Timely and accurate tracking of inventory levels helps businesses avoid unnecessary costs and ensures that products are in the right place at the right time. It also aids in identifying slow-moving items and preventing obsolescence. In essence, good inventory management streamlines operations, reduces costs, and enhances overall efficiency, contributing to the success of a business.
If you opt for inventory management in spreadsheets we have a free and completely ready‑to‑use spreadsheet template to help you manage your processes.
How Inventory Management Mistakes May Harm a Company
Inventory management mistakes can seriously harm your company’s bottom line. Failure to prioritize products based on demand can impact sales and customer satisfaction. Additionally, neglecting to conduct regular audits may result in outdated items remaining in stock, further hindering profitability.
Neglecting the need to implement a robust tracking system may contribute to theft and shrinkage, to the necessity to do tedious work, and to the decrease of the motivation of all employees in the company. Various inventory mistakes may also lead to low employee productivity.
Let’s examine the most widely spread inventory management mistakes and learn how to overcome them.
Mistake 1. Overstocking
Overstocking is a common challenge in inventory management that occurs when businesses hold excessive amounts of stock beyond what is needed. This can tie up valuable capital, lead to storage issues, and result in the risk of products becoming obsolete.
To address overstock problems, it’s essential to regularly analyze sales trends, set realistic reorder points, and establish effective communication channels with suppliers. Implementing a just‑in‑time inventory system, where products are restocked as needed, can help businesses maintain optimal stock levels, reduce carrying costs, and improve overall efficiency in inventory management.
Mistake 2. Understocking
Understocking is a common hiccup in inventory management where businesses don’t have enough products to meet customer demand. This mistake can lead to lost sales, unhappy customers, and a damaged reputation.
To tackle understock issues, it’s crucial to implement effective forecasting tools and regularly analyze sales trends. Utilizing historical data and staying updated on market fluctuations can help businesses predict demand more accurately. Additionally, maintaining open communication with suppliers and having a flexible replenishment strategy ensures that products are restocked promptly. By addressing understocking proactively, businesses can enhance customer satisfaction and maximize their revenue potential.
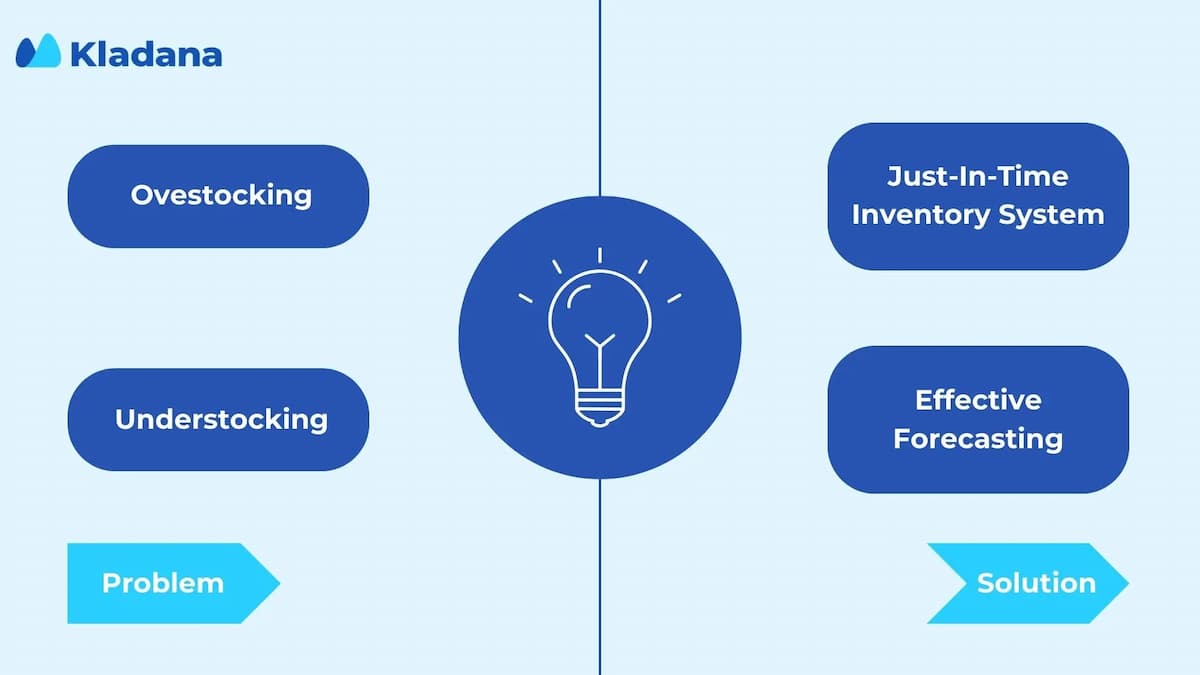
Mistake 3. Poor Inventory Visibility
One common mistake in inventory management is poor visibility, where businesses struggle to accurately track their stock levels. This lack of clarity can lead to overstocking or stockouts, causing losses of money and customer dissatisfaction.
The solution to this problem lies in implementing advanced inventory management systems that offer real‑time tracking and automation. By utilizing barcode scanners, RFID (Radio Frequency Identification) technology, or reliable software, businesses can gain a clear and instant view of their inventory, helping them make informed decisions, prevent excess stock, and ensure products are always available when needed. Improved visibility not only enhances efficiency but also contributes to overall business success.
Mistake 4. Unsuitable Inventory Storage
One common mistake in inventory management is the unsuitable storage of goods. Storing items haphazardly or without proper organization can lead to difficulties in locating and retrieving products when needed. This can result in delays, errors, and even financial losses for businesses.
The solution to this problem lies in implementing a systematic and organized storage system. Categorizing products based on factors like size, demand, or expiry date can make it easier to locate and manage inventory efficiently.
Investing in shelving, labeling, and digital tracking systems can further enhance organization, ensuring that items are stored in the right place and can be easily accessed when required. By addressing the issue of unsuitable inventory storage, businesses can streamline their operations and improve overall efficiency in managing their stock.
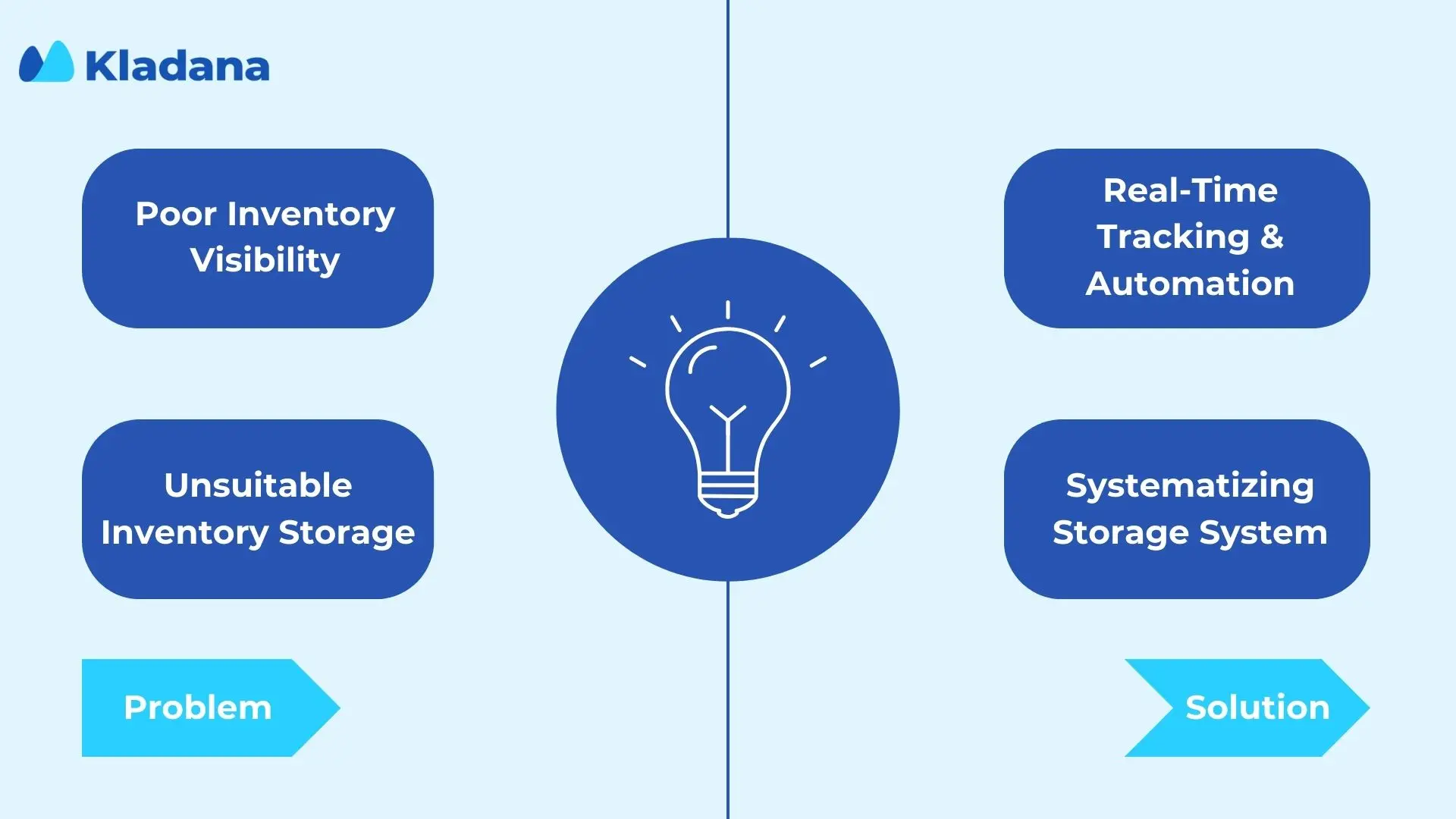
Mistake 5. Prevalence of Manual Processes
Manual processes in inventory management continue to be a crucial challenge for many businesses. Relying on manual methods such as spreadsheets and handwritten logs can lead to errors, inefficiencies, and increased risk of stockouts or overstock situations.
The solution to this problem lies in embracing modern inventory management software. By automating tasks like order processing, tracking stock levels, and generating reports, businesses can significantly reduce human errors and streamline their operations. Implementing a digital solution not only enhances accuracy but also provides real‑time insights, helping organizations make informed decisions to optimize their inventory levels and overall efficiency.
Read‑alikes
Free Inventory Management Software 2025: Top 20 Solutions for Small Businesses
Inventory Counting: Step‑by‑Step Guide on How to Conduct and Access the Results
Inventory Management in Excel: Free Template and a Step‑by‑Step Guide
Mistake 6. Lack of Communication and Limited Skills
A prevalent challenge that often leads to costly errors in inventory management is the lack of communication and limited skills among the employees. When information fails to flow seamlessly across departments, discrepancies arise, resulting in inaccurate stock levels and delayed orders. Moreover, inadequate skills in utilizing inventory management software or understanding the intricacies of supply chain processes can compound these issues.
To tackle this, organizations must prioritize fostering open lines of communication through regular meetings and streamlined reporting systems. Additionally, investing in training programs to enhance the skills of the workforce ensures that everyone is well‑equipped to navigate the complexities of inventory management, minimizing errors and optimizing overall efficiency. By addressing these issues, businesses can build a foundation for a more robust and error‑resistant inventory management system.
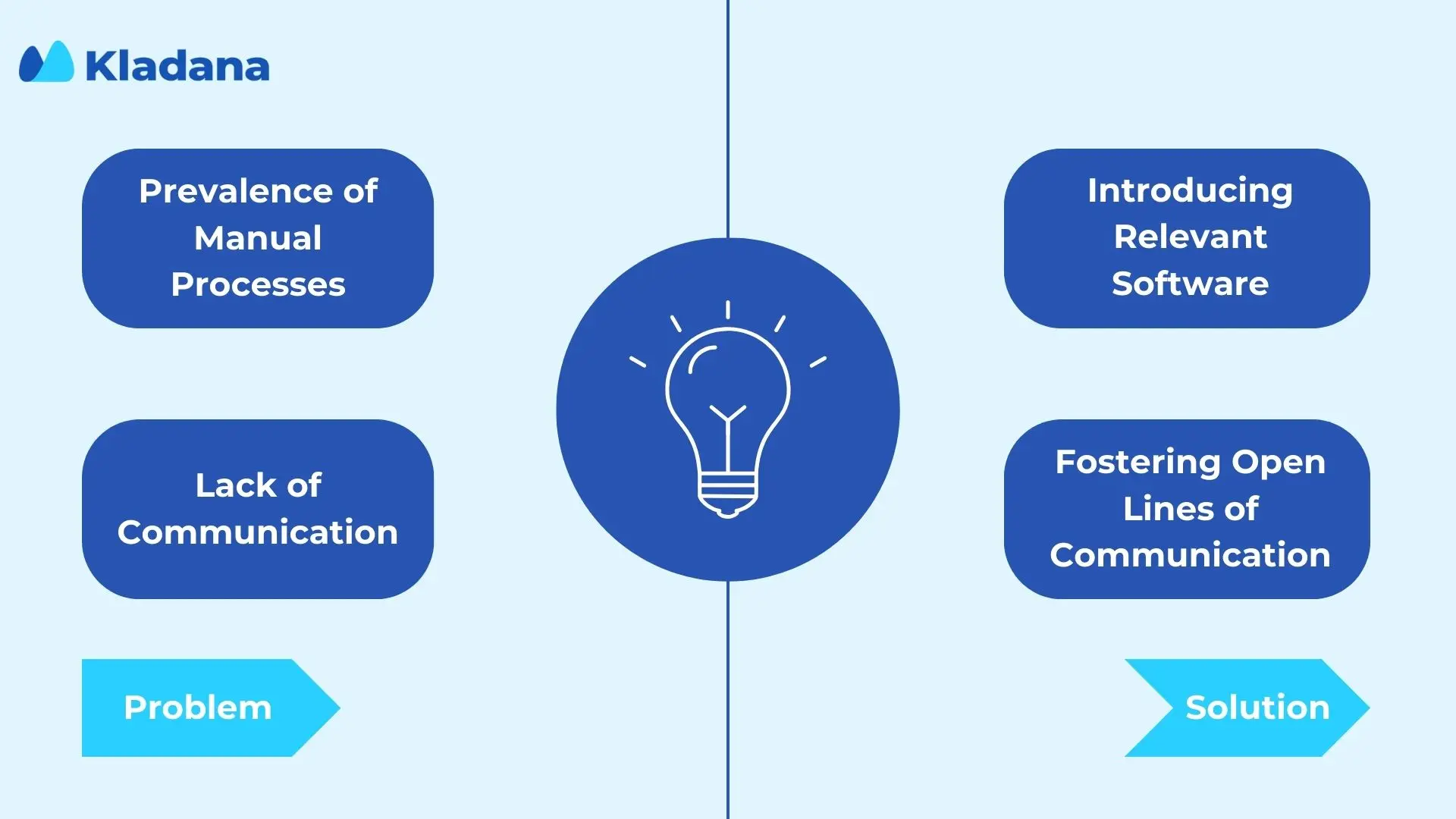
Mistake 7. Inadequate Integration with Other Systems
One common mistake in inventory management is inadequate integration with other systems. When your inventory system operates in isolation from other crucial business systems like sales, procurement, and accounting, it can lead to inefficiencies and errors.
The solution lies in implementing seamless integrations between your inventory management system and other relevant software. This ensures real‑time data exchange, allowing for accurate and up‑to‑date information across all departments. By fostering better communication between systems, you can streamline processes, minimize errors, and enhance overall efficiency in managing your inventory. Integration is key to achieving a cohesive and well‑coordinated approach to inventory management, preventing the pitfalls associated with inadequate system connections.
Customer Stories
Unicorn Natural Products Manufacturing: a Journey from Spreadsheets to ERP
Cura Pharmaceuticals Manufacturing: Increased Data Accuracy & Business Workflows in 6 Months
Artisanté: How to Streamline Chocolate & Coffee Manufacturing Management in Half a Year
Mistake 8. Growing Competition
Intensifying competition in the sphere of business has sharpened the challenges associated with inventory management.
The remedy to this predicament lies in the adoption of advanced technology and the implementation of robust inventory management systems. Through the integration of up‑to‑date software and automation tools, businesses can access real‑time insights into their inventory levels, streamline procurement processes, and optimize stock levels. This not only enhances operational efficiency but also empowers businesses to meet customer demands more effectively, ultimately providing a competitive edge in the market.
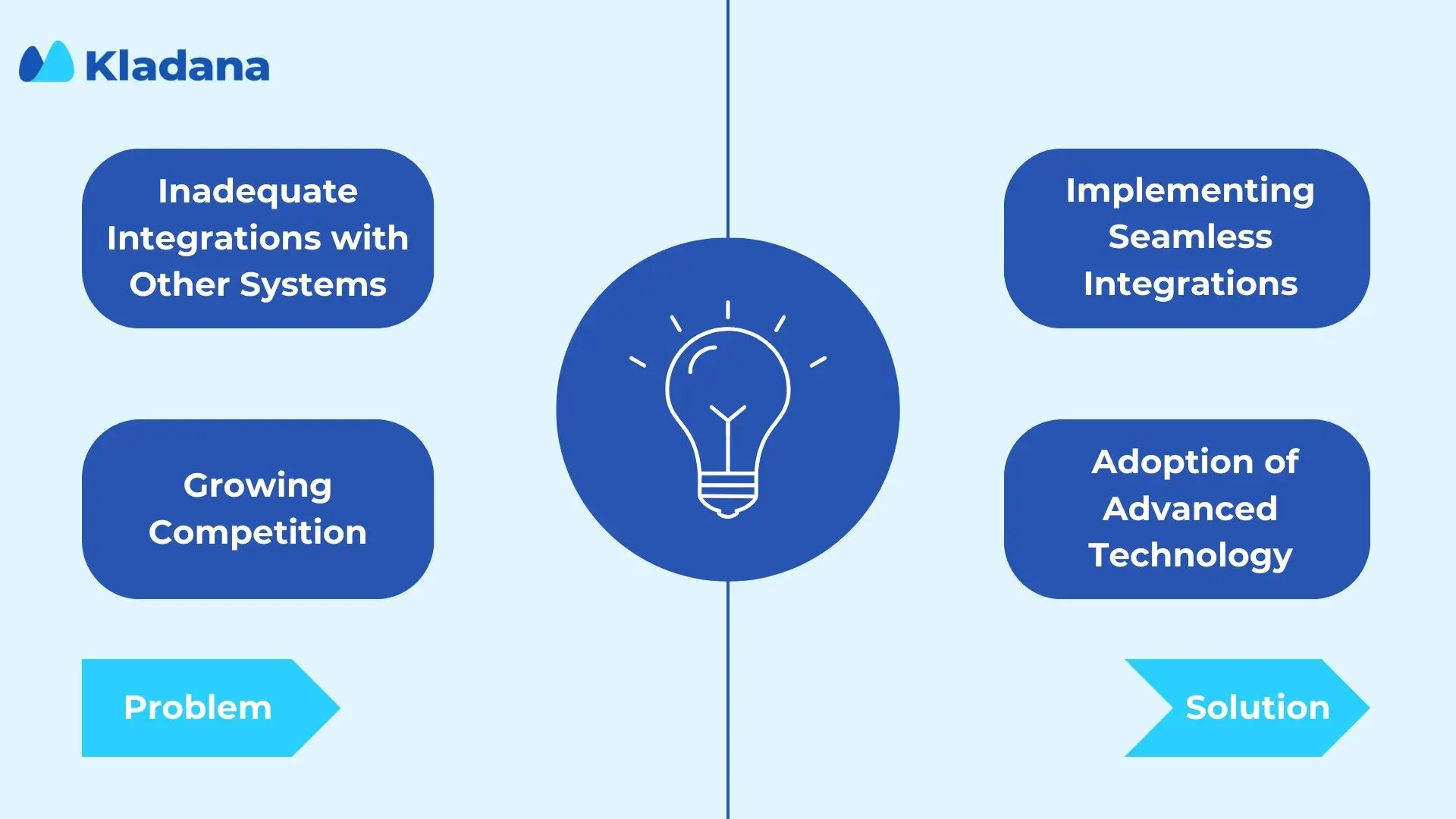
Mistake 9. Fluctuating Customer Demand
One common challenge in inventory management is dealing with the fluctuation of customer demand. Businesses often face the dilemma of unpredictable shifts in the market, leading to overstocking or stockouts.
To address this issue, implementing a robust demand forecasting system is crucial. By analyzing historical sales data, market trends, and customer behavior, businesses can make informed predictions about future demand.
Additionally, regular updates and adjustments to forecasts based on real‑time data can help optimize inventory levels. This proactive approach enables businesses to respond swiftly to changes in customer demand, ensuring a more efficient and cost‑effective inventory management system.
Mistake 10. Supply Chain Complexity
Supply chain complexity poses a significant challenge in effective inventory management. The intricate web of suppliers, distributors, and various stakeholders can lead to communication breakdowns and delays. Misalignment in production schedules, fluctuating demand, and unforeseen disruptions can compound the intricacy.
To address these issues, implementing advanced technologies like cloud‑based inventory management systems, data analytics, and automation can provide a solution. These tools enhance communication, streamline processes, and offer better insights for forecasting demand accurately. By leveraging technology to simplify the supply chain, businesses can optimize inventory levels, reduce costs, and improve overall efficiency in inventory management.
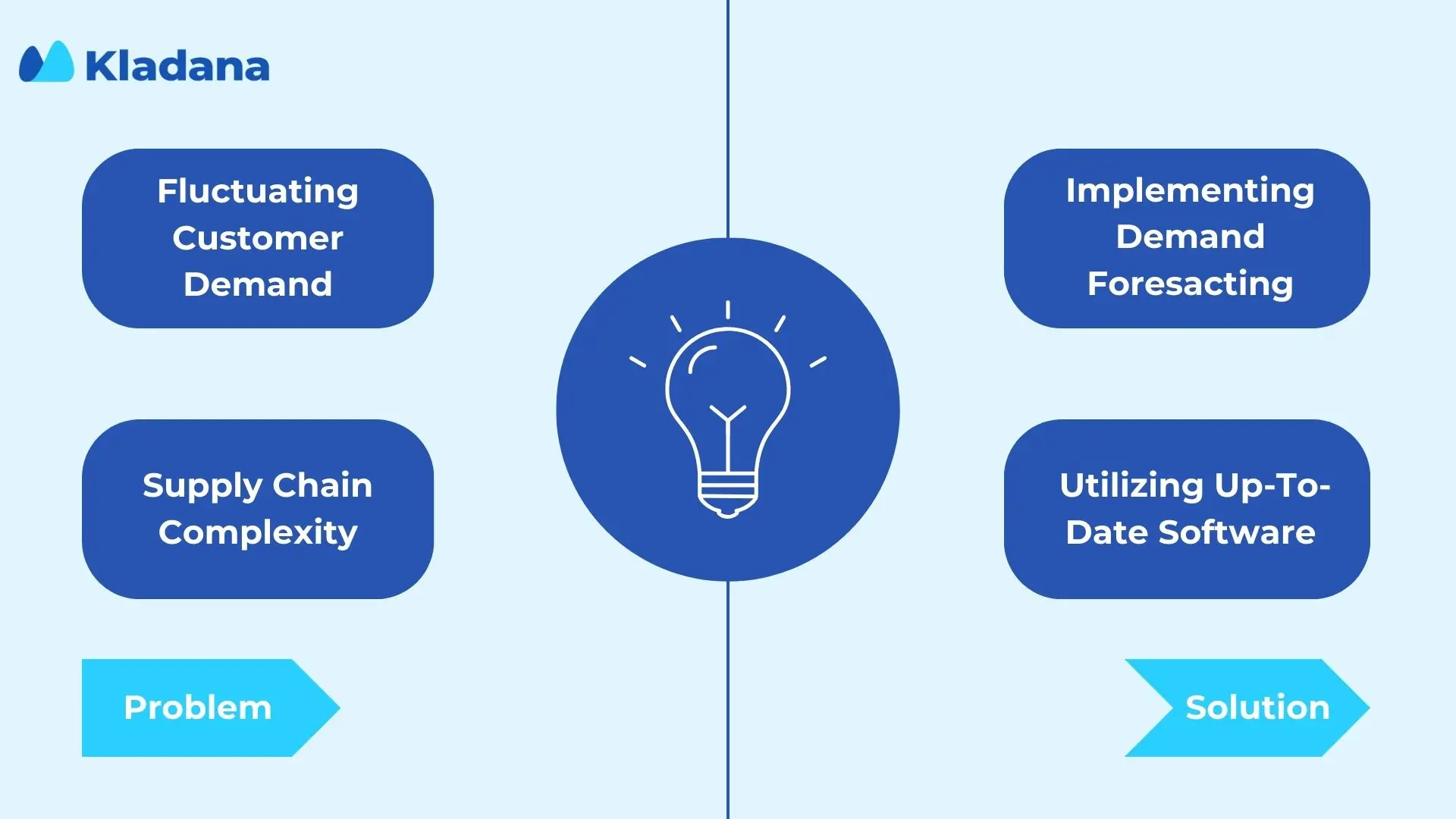
Solutions that Automate Processes and Help Avoid Mistakes
To tackle inventory management challenges, automated solutions emerge as game‑changers. Implementing barcode systems ensures accurate tracking, reducing the risk of errors in product counts. Advanced software provides real‑time updates on stock levels. Automated reorder alerts prevent stockouts and overstock situations and optimize inventory turnover.
Criteria | Manual Inventory Management | Software Automation for Inventory Management |
Accuracy |
Prone to human errors, such as data entry mistakes and miscalculations. |
Offers high accuracy through automated data input, reducing the risk of human errors. |
Speed |
Slow and time-consuming, especially for large inventories. Counting and updating records is a time-intensive process. |
Rapid and efficient, automating tasks like real-time updates and order processing, leading to faster operations. |
Visibility |
Limited visibility into real-time stock levels, making it challenging to respond quickly to demand fluctuations or stockouts. |
Provides real-time visibility into inventory levels, facilitating better decision-making and preventing stockouts or overstock situations. |
Scalability |
Difficult to scale for growing businesses, as manual processes become more complex and time-consuming. |
Highly scalable, easily adapting to the increasing volume of products and transactions as a business expands. |
Cost Efficiency |
Labor-intensive and may incur higher labor costs over time. Additionally, errors can lead to financial losses. |
Initially, there may be an investment in software implementation, but the long-term savings from increased efficiency and reduced errors contribute to cost-effectiveness |
Cloud‑based platforms centralize data, enhancing accessibility and minimizing the chance of discrepancies across multiple locations. These solutions not only streamline operations but also contribute to minimizing manual errors, enabling businesses to maintain efficient and error‑free inventory management.
Start your introduction to cloud‑based systems by trying Kladana for free, an ERP specifically crafted for SMEs. It’ll help you to avoid the wide‑spread inventory management mistakes:
- Real-Time Visibility: Kladana provides real‑time visibility into inventory levels, enabling businesses to track stock levels accurately and make informed decisions promptly.
- Automation of Processes: With Kladana, manual tasks are minimized, reducing the likelihood of human errors in data entry and order fulfillment. Automation streamlines processes, improving accuracy and efficiency.
- Centralized Data: The solution centralizes data, ensuring that all departments have access to up‑to‑date information. This minimizes the risk of discrepancies between different parts of the business, fostering a unified approach to inventory management.
- Forecasting and Analytics: The system utilizes advanced forecasting and analytics tools, helping businesses anticipate demand patterns and optimize stock levels. This proactive approach minimizes the risk of overstocking or stockouts.
- Enhanced Collaboration: Cloud‑based ERP facilitates collaboration among different departments, suppliers, and partners. This improved communication helps in addressing issues promptly.
The investment in automation software often pays off by streamlining operations, minimizing errors, and allowing businesses to focus on strategic growth rather than routine inventory tasks.
Frequently Asked Questions on Typical Inventory Management Mistakes
Read about why people often make multiple mistakes while managing inventory and the potential consequences that may arise as a result.
What is bad inventory management?
Bad inventory management refers to the inefficient control and monitoring of a company’s stock. This can manifest in overstocking, understocking, inaccurate records, or outdated tracking systems. Essentially, it’s a failure to align the quantity and timing of goods with actual demand, leading to financial losses, customer dissatisfaction, and operational inefficiencies.
Why is inventory management so complicated?
Inventory management is complex due to the dynamic nature of business operations. Factors such as fluctuating demand, supplier delays, market trends, and unforeseen events contribute to the intricacies. The need to strike a delicate balance between having enough stock to meet customer demands while avoiding excess that ties up capital makes it a challenging task. Additionally, the integration of technology and evolving supply chain models adds another layer of complexity.
Why is inventory management a high‑risk endeavor?
Inventory management carries inherent risks because it directly impacts a company’s financial health and customer satisfaction. Overstocking can lead to excessive holding costs and potential obsolescence while understocking risks stockouts and lost sales. The volatility of markets and unforeseen disruptions, like natural disasters or supply chain issues, amplify these risks. Inaccurate data, insufficient monitoring, and delayed responses to changing conditions can exacerbate the potential for losses.
How does poor inventory management affect a company’s bottom line?
Poor inventory management directly impacts a company’s bottom line through various channels. Excessive inventory ties up capital, leading to increased holding costs, while stockouts result in lost sales and potential damage to customer relationships. Inaccurate forecasting can lead to overstocking or understocking, both of which affect profit margins. Inefficient inventory practices can also lead to increased operational costs and decreased overall business efficiency.
What steps can businesses take to mitigate inventory management challenges?
Mitigating inventory management challenges requires a strategic approach. Implementing advanced inventory tracking systems, adopting data analytics for demand forecasting, maintaining transparent communication with suppliers, and regularly auditing inventory processes are essential steps. Embracing lean inventory principles and leveraging technology, such as automation and AI, can enhance efficiency and reduce the risk of human error. Regularly reviewing and adjusting inventory management strategies in response to market changes is crucial for sustained success.
Check our blog for more articles on organizing business processes. Click the link below to access our complete blog and explore other subjects chosen specifically for helping small and medium‑sized businesses.